Andon
Andon is a visual management tool that highlights the status of operations in an area at a single glance and that signals whenever an abnormality occurs.
An andon can indicate:
- production status — for example, which machines are operating
- an abnormality — for example, machine downtime, a quality problem, tooling faults, operator delays, and materials shortages),
- needed actions, such as changeovers.
Organizations can also use andon to display the status of production in terms of the number of units planned versus actual output.
A typical andon, which is the Japanese term for “lamp,” is an overhead signboard with rows of numbers corresponding to workstations or machines. A number lights when either:
- a machine sensor detects a problem, which automatically trips the appropriate light or
- an operator pulls a cord or pushes a button.
The illuminated number summons a quick response from the team leader. Colored lighting on top of machines to signal problems (red) or normal operations (green) is another type of andon.
Andon and Fixed-Position Stop
The fixed-position stop system that Toyota uses in its final-assembly lines is very famous and very effective. Whenever an operator encounters any problem, he or she pulls a rope, which will cause the production line to stop, not immediately, but after the product reaches a predetermined position. Efforts are made to bring the line back into normal operation by solving the problem immediately, but if the problem stays unsolved within the cycle, the conveyor stops at the fixed position.
If the operation having a problem could stop at any position, the work of every other operation would be interrupted. Consequently, this might cause operator error, such as incorrect assembly. Instead, stopping at the fixed position (i.e., the end of each workstation) will not negatively affect other workstation operations in safety and quality. With this method, stoppage time is minimized yet the jidoka concept is maintained because abnormalities are remedied and defects never passed on.
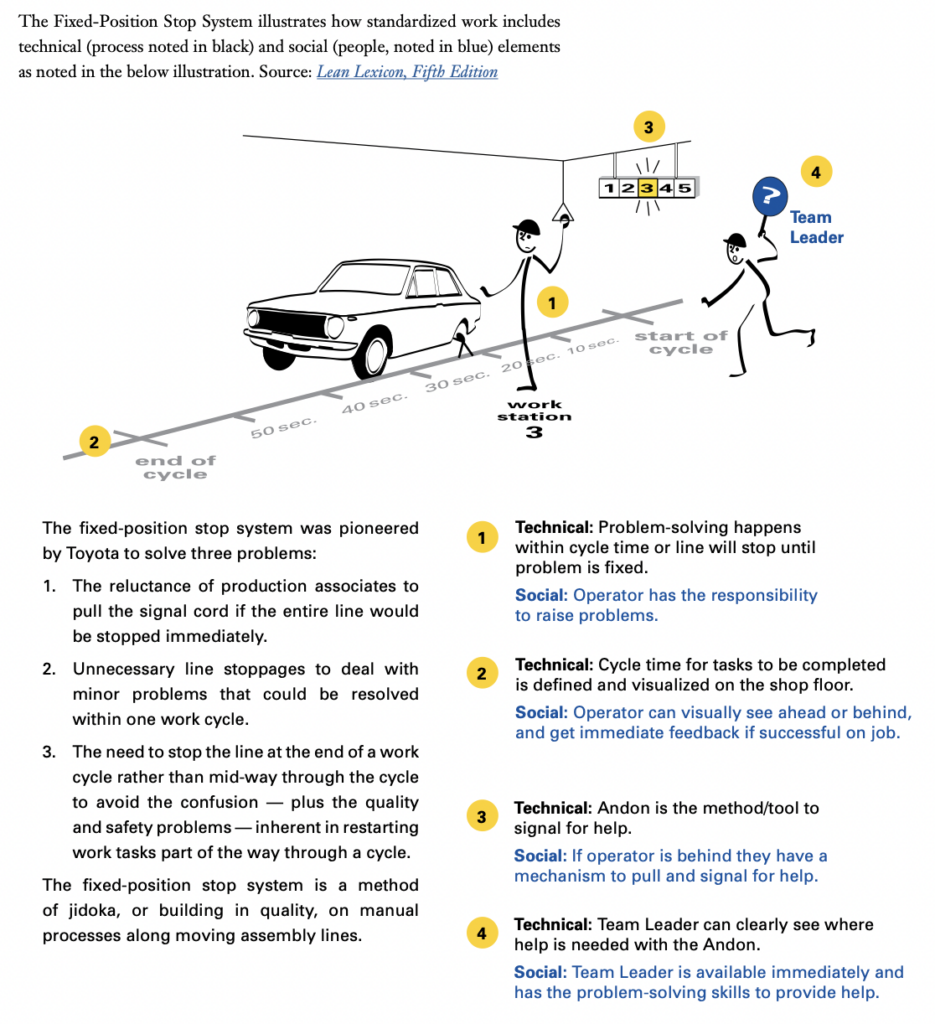

100 Years of Innovation in the Work: an Explanation of Fixed-Position Stop and Andon
Additional Resources
Article
Gemba and Quality
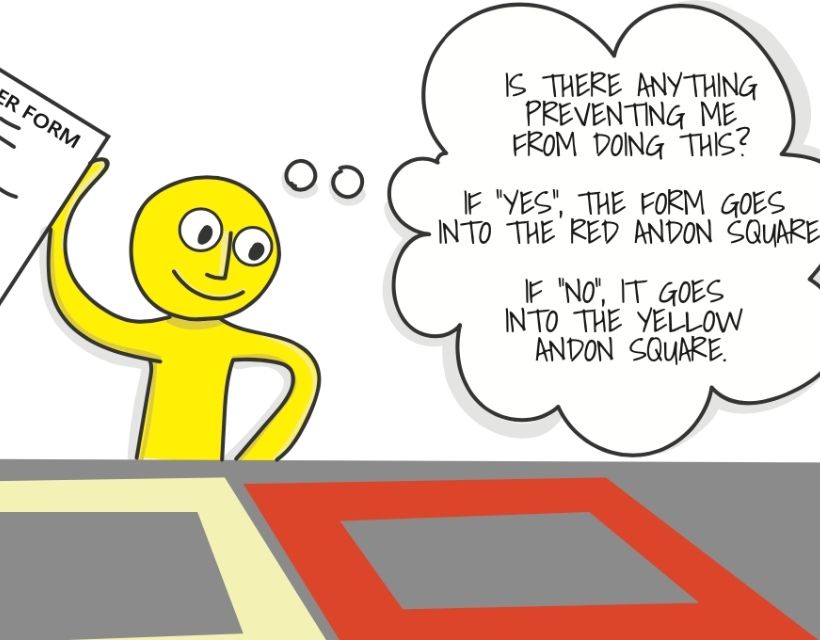
Article
Andon Squares — 5S in the Office
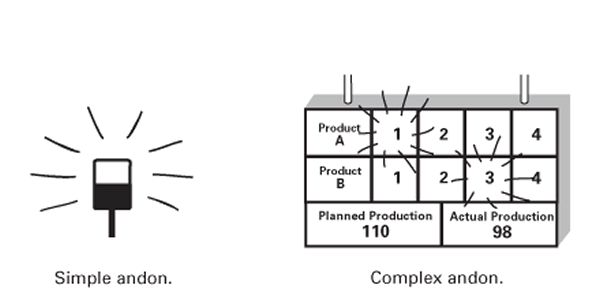