In a relay race, the winning team isn’t the one that runs the fastest leg, but the one that runs fastest start to finish without dropping the baton. In business, the winning supply chain isn’t the one with the most efficient operational silos, but the one that is most efficient end to end, especially at the handoffs.
In other words, you can have four incredible athletes running a relay race, but if they don’t get the handoffs right, they don’t win. In your supply chain, the handoffs also are where you’re most likely to drop the “baton.”
Handoffs occur where supplier processes connect with yours, where your processes connect with customers, where wholesalers connect with retailers, etc. Processes at handoffs often lack visibility and discipline.
The Scope of End to End Supply Chain
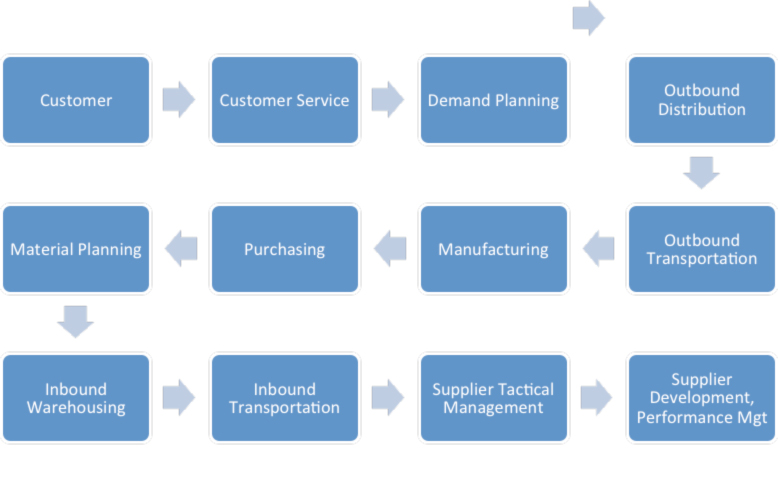
For instance, a retailer focused on lowering transportation costs may order in large quantities. So the handoff between the retailer and supplier is at the transportation function, which will be teeming with waste because the supplier is building in batches to meet truckload quantities although such quantities have nothing to do with actual customer demand.
Another example is a manufacturer that doesn’t share production forecasts or lacks a disciplined production schedule. Suppliers must guess what to build, which creates a lot of waste when they guess wrong.
Guiding Principles for Rethinking Supply Chains
Forward thinking organizations now are focusing on the total cost of fulfillment, end-to-end, because they are recognizing that wastes don’t exist so much inside the functions of the supply chain but rather at the interfaces where each node connects with the next node. What that means is that these leaders are now looking at their supply chains from the consumption of their product by customers all the way upstream through distribution, through manufacturing, and through inbound logistics to their supply base.
As companies do the end-to-end analysis, they begin to question off-shoring strategies, but the goal isn’t to offshore or near shore or repatriate. The goal is to have the most efficient end-to-end supply chain.
Because supply chains are so long and dynamic, you’ll need the following eight lean principles to guide you in analyzing and improving handoffs with suppliers and customers:
- Eliminate the seven types of waste in the fulfillment stream so that only value remains:
• System complexity: elaborate scheduling systems and working around disconnects between the formal schedule and actual needs
• Lead time: taking too much time from one step to the next
• Transport: excessive conveyance among facilities and companies
• Space: excessive space for storage is waste
• Inventory: at any point in the fulfillment stream
• Wasted human effort: examples are rework, confusion, and excess motion
• Packaging: the wrong types of goods in the wrong quantities - Make customer consumption visible to all members of the fulfillment stream so it’s easier for every participant to plan work ahead based on the pull of customer demand.
- Reduce inbound and outbound logistics lead time to get orders to the customer faster.
- Create level flow so goods and information move in a predictable, consistent, and uninterrupted manner based on actual demand.
- When level flow is not possible, use pull systems in which each downstream activity signals its need to the next upstream activity.
- Increase velocity and reduce variation so you can more easily adjust delivery to meet actual customer consumption.
- Collaborate and use process discipline so all participants in the value chain are identifying problems for root cause analysis.
- Focus on total cost of fulfillment. Be careful not to make decisions that benefit one part of the supply chain at the expense of another.
The lean supply chain relentlessly focuses on lead-time reduction by eliminating all non-value creating activities (waste). This is accomplished through rigorous process discipline, inventory reduction, and first-time quality.
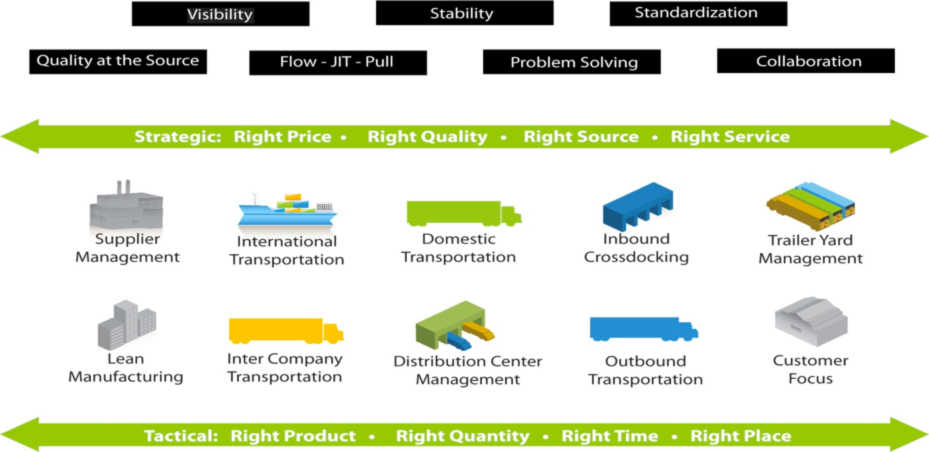
So, if your company has done lean improvements within your four walls and is wondering why it can’t get more improvements, the answer is that the greatest opportunities are now in the supply chain – where the baton gets dropped.
Next Step: Build Leadership Skills for the Changing Nature of Work
As the founding CEO of LeanCor Supply Chain Group, Robert has seen the technical, social, and political changes roiling the world’s supply chains. Now changes such as automation, artificial intelligence, and the Internet of Things are shaking up the very nature of work.
Lean Warehousing and Distribution Operations
Improve a distribution center's efficiency, quality, safety, and space utilization.