Most students of engineering learn that the game is about control. They are taught a lot about predictive problem solving, with relatively little about adaptive problem solving. In their book Your Leadership Edge, Ed O’Malley and Amanda Cebula make this critical distinction. In predictive problem solving, the expert engineer uses analytic means to clearly define the problem and find the root cause. This leads to a clear solution the experts have great confidence in, before actually trying it. Then it’s simply a matter of implementing something and confirming that it works as expected. We can think of this as one Plan-Do-Check-Act Cycle, where the check is simply confirming what the experts already believe they know.
Adaptive problem solving is more circumspect. Even the problem definition is unclear and can take extensive investigation and benefits from direct observation of the actual processes as they are carried out. The problem solver values the input of key stakeholders who experience the problem in different ways. The “Do” stage becomes part of the investigation experimenting with alternative ideas. Each experiment is its own small PDCA cycle with the result more learning which informs the next experiment. The problem solver is learning their way to the solution instead of predicting their way.
The problem solver is learning their way to the solution instead of predicting their way.
Problems in textbooks can be solved if you put the right numbers into the right equations. In operations research, if you specify the function properly, you can optimize the system, or there is a recognition that some problems cannot be solved analytically and therefore, you need a more data-hungry approach like simulation. Still, the idea is that through simulation, you solve the problem before needing to deal with the messiness of the real world.
We live in a complex world. At Toyota, the starting assumption is that most are messy. For example, we’ve studied Toyota’s approach to prototyping and found they are more likely than competitors to encourage a lot of rapid physical prototyping… even in the study stage before they have designed the full vehicle. The concept of learning by doing at the gemba (the place where the real, value-creating work gets done) is deeply engrained in Toyota culture. This is powerful because it reflects a humble attitude of accepting uncertainty. Leaders think, “We do not know, but we will develop our best guess and then try something.”
The concept of learning by doing at the gemba is deeply engrained in Toyota culture…it reflects a humble attitude of accepting uncertainty.
Toyota is famous for its Toyota Production System which has mistakenly been viewed by many as a set of tools to deliver parts just-in-time and stop and fix quality problems. The Toyota Product Development System similarly has led to a plethora of tools like obeya, value stream mapping, set-based design, and various checklists. But underlying the effective use of these tools is a way of thinking that Toyota refers to as problem solving. In an earlier era, it was talked about as scientific thinking. (The famous Plan-Do-Check-Act cycle can be viewed as one large single loop of predictive problem solving and many smaller loops of adaptive problem solving.)
My colleague Mike Rother has codified this concept of scientific thinking in what he calls Toyota Kata. The goal is to develop practice routines that essentially push the learner in the direction of more adaptive problem solving, instead of assuming all their predictions are correct. A big problem is broken into a series of smaller problems, and we experiment our way to the “next target condition,” then the next, then the next… You get the idea. I taught this approach in a graduate course with industrial and operations engineering graduate students at the University of Michigan. Most of my students had a propensity to want to analyze and analyze and analyze data to find the perfect solution before actually testing any ideas. Sound familiar? But through Toyota Kata, they eventually discovered the value of rapid experimentation. In the end, the learning was profound.
I am not suggesting that we abandon all the means we have at our disposal to codify knowledge and come up with predictive algorithms. At the very least, this may get us close to a good solution that can be refined through adaptive problem solving. But I do think a humbler attitude toward the complexity we wrestle with every day is a healthy step forward. Leading and learning this way may take more time and patience. It also becomes easier when we value the knowledge of those close to the gemba.
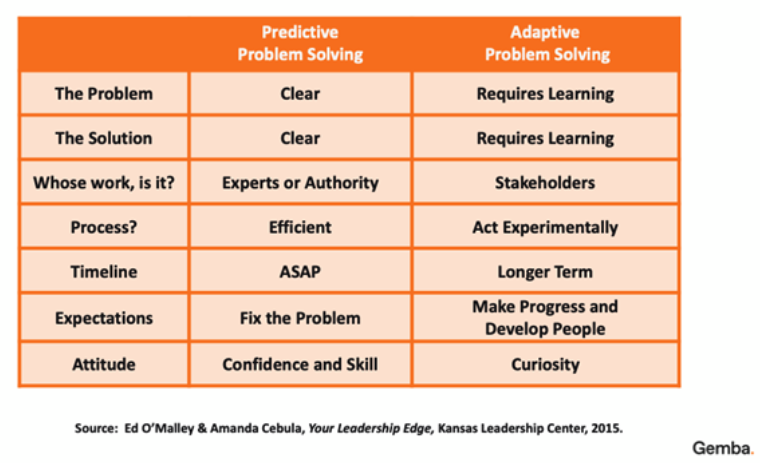
Designing the Future
An Introduction to Lean Product and Process Development.