Plan, Do, Check, Act (PDCA)
PDCA is an improvement cycle based on the scientific method of proposing a change in a process, implementing the change, measuring the results, and taking appropriate action. It also is known as the Deming Cycle or Deming Wheel after W. Edwards Deming, who introduced the concept in Japan in the 1950s. It is also known as PDSA, where the “S” stands for “study”.
The PDCA cycle has four stages:
- Plan — determine goals for a process and needed changes to achieve them.
- Do — implement the changes.
- Check — evaluate the results in terms of performance
- Act — standardize and stabilize the change or begin the cycle again, depending on the results
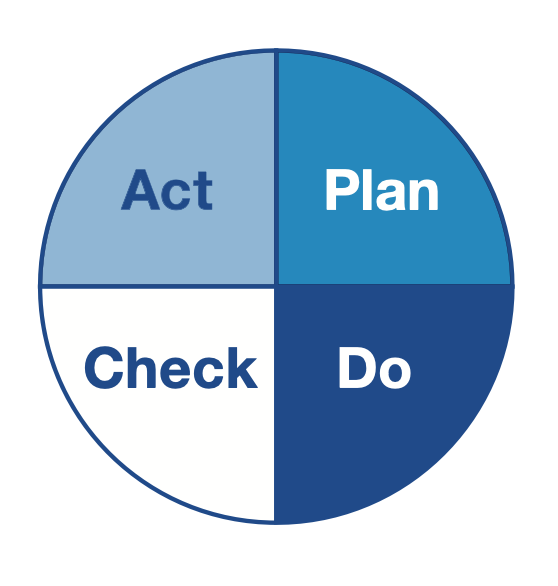
PDCA is the foundation of continuous improvement or kaizen. Leaders set targets (plan) against a stable baseline of performance. Teams implement improvements (Do) to achieve the targets. Then they measure (Check) the change to evaluate performance against the target. If the team has achieved a measurable gain, it standardizes (Act) the new method by updating the standardized work. This ensures the improvement is stable.
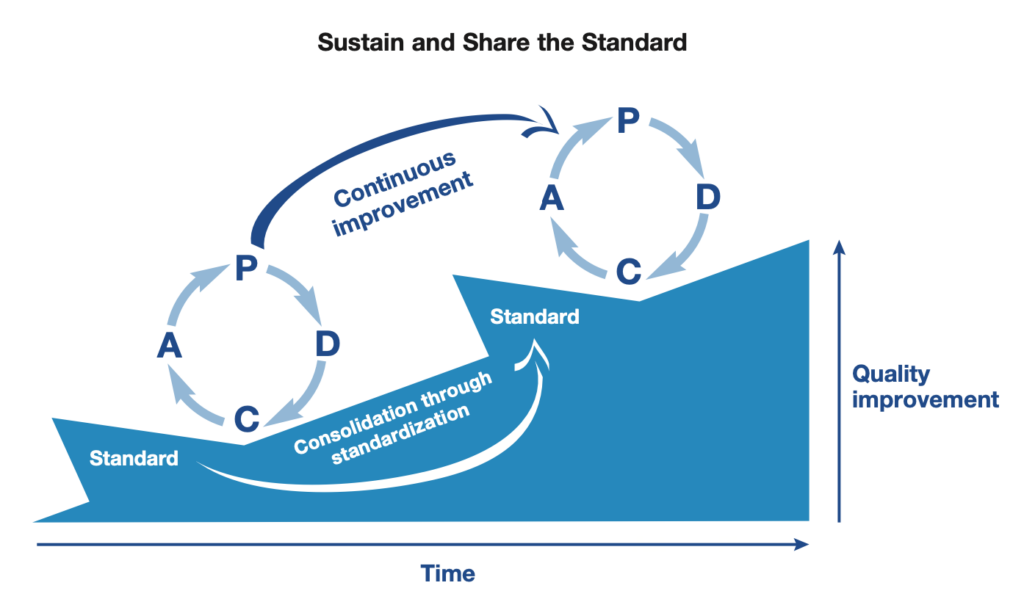
History of PDCA
Walter A. Shewhart was the first to develop a repeating cycle for improvement dubbed the Shewhart Cycle:
- Specify
- Produce
- Inspect
Edward Deming expanded the Shewart cycle into a four-step pattern for Japanese audiences. The Deming cycle related heavily to the concept of product quality, innovation, and learning-by-doing over the entire life cycle of a product.
Specifically, the Deming cycle runs:
1. Design the product with appropriate testing.
2. Make the product and test it in production and in the lab.
3. Sell the product to the market.
4. Test the customer experience and redesign for improvement.

In 1951, the Japanese Union of Scientists and Engineers (JUSE) altered Deming’s framework into the more recognizable PDCA cycle. Although well over half a century has passed since the introduction of the Deming cycle to executives in Japan, most open-ended approaches still seek to repeat learning cycles as rapidly as possible, for obtaining customer feedback and making improvements in all pertinent areas.
The language may change slightly, but the basic thinking has not changed much. Consider the three-phase concept—Build, Measure, Learn—popularized by Eric Ries in his book, The Lean Startup. His iterative process is fundamentally similar to both the original Shewhart and Deming cycles. Words may change or be slightly altered, but the timeless, classic concepts stay the same.
Additional Resources
- Test Your PDCA Thinking By Reading Your A3 Backwards
- Create a Real A3, Do More Than Fill In Boxes
- Hazards at the Huddle Board: How to Coach a Team Away from “Fast Thinking” to Disciplined PDCA
- Practical Guidance for Using Humble Inquiry in PDCA Problem Solving and Coaching
- The Key to Lean — Plan, Do, Check, Act!
- Four Types of Problems — Art Smalley
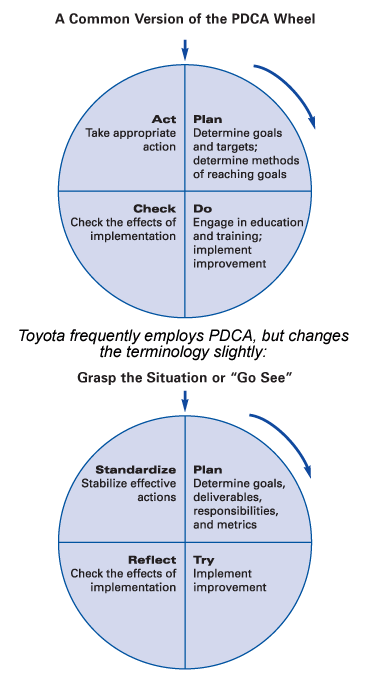