Takt Time
Takt time is a calculation of the available production time divided by customer demand.
For example, if a widget factory operates 480 minutes per day and customers demand 240 widgets per day, takt time is two minutes. Similarly, if customers want two new products per month, takt time is two weeks. The purpose is to precisely match production with demand. It provides the heartbeat of a lean production system.
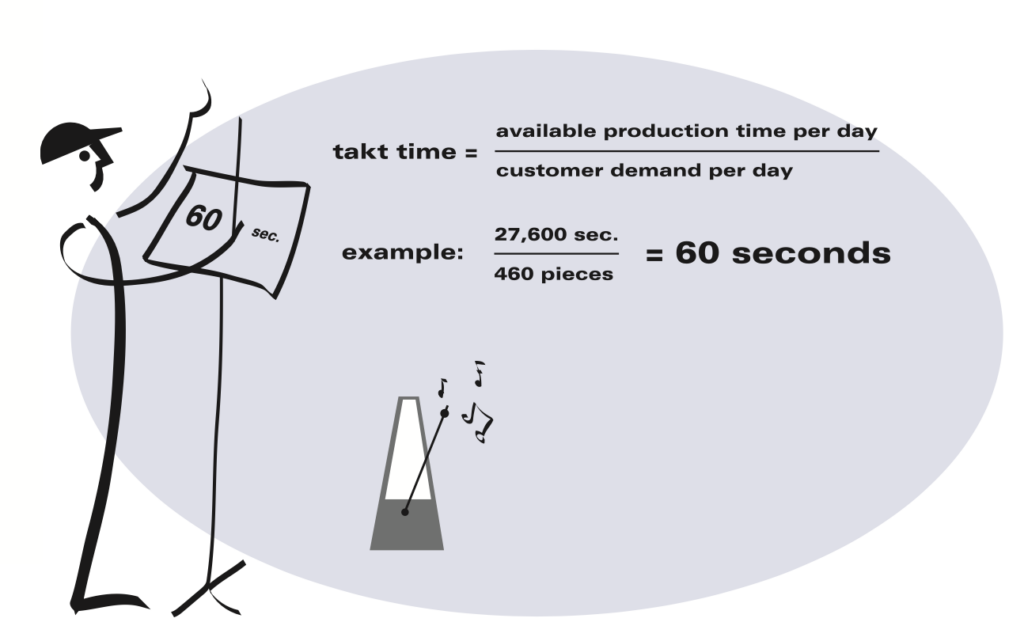
Takt first was used as a production management tool in the German aircraft industry in the 1930s. (Takt is German for a precise interval of time such as a musical meter.) It was the interval at which aircraft were moved ahead to the next production station. The concept was widely utilized within Toyota in the 1950s and was in widespread use throughout the Toyota supply base by the late 1960s. Toyota typically reviews the takt for a process every month, with a tweaking review every 10 days.
The purpose of takt time is to precisely match production with demand. It provides the heartbeat of a lean production system.
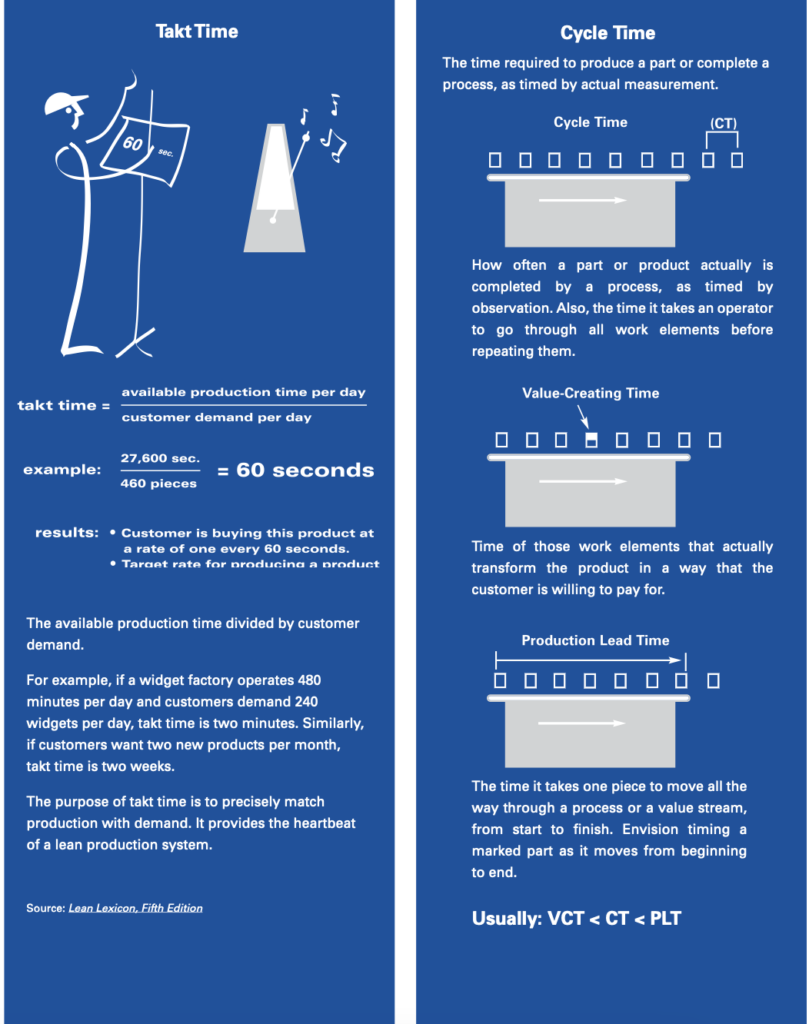
Additional Resources
Coaching Effectively Within Takt Time
When time is of the essence and work just needs to be done, how do you help someone improve their work or solve a problem quickly? Jeff Smith shares an example from the shopfloor.
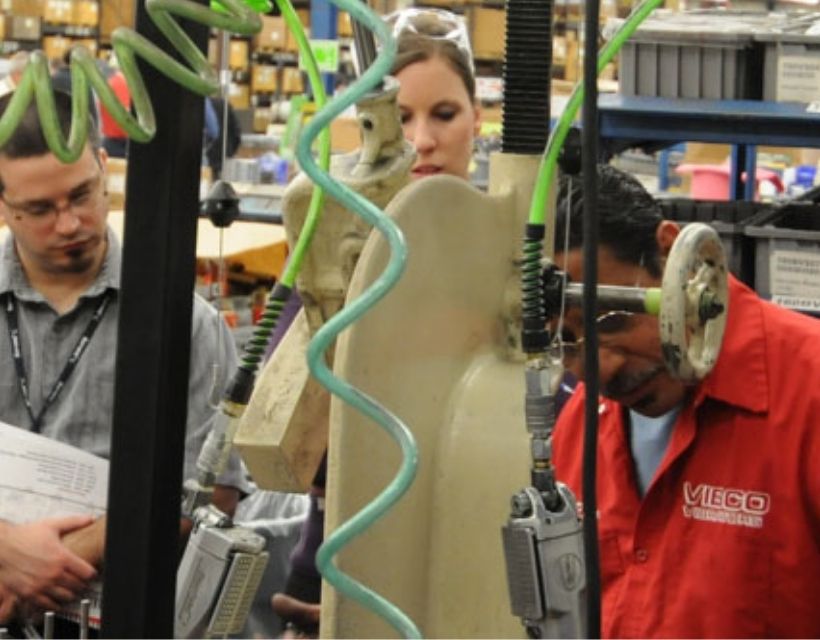
Ask Art: Why is Takt So Important in a Lean Turnaround?
Takt represents the beat of the customer, or, the rate of demand, says Art Byrne: “As the primary focus of the lean company is delivering more value to its customers than its competitors can, then conformity to their demands in a quick, efficient way is the main driver. Takt time is therefore what sets the tone for everything else.”
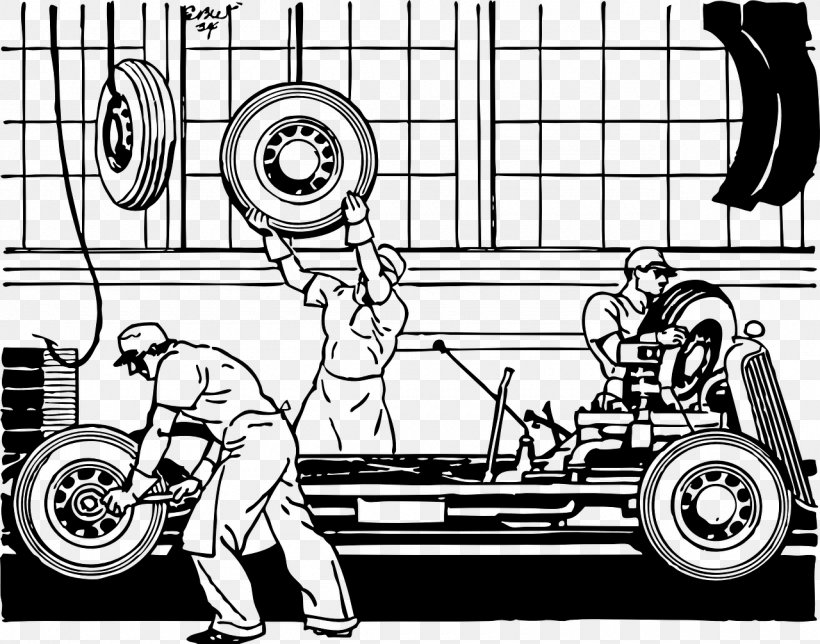
Takt Thinking for a Low-Volume High-Mix Company
Dear Gemba Coach: Our company produces custom products that cannot be easily forecast in terms of when they will be ordered, and in what format. How can a company facing high-mix, low-volume, and unstable demand establish a production system that uses takt?
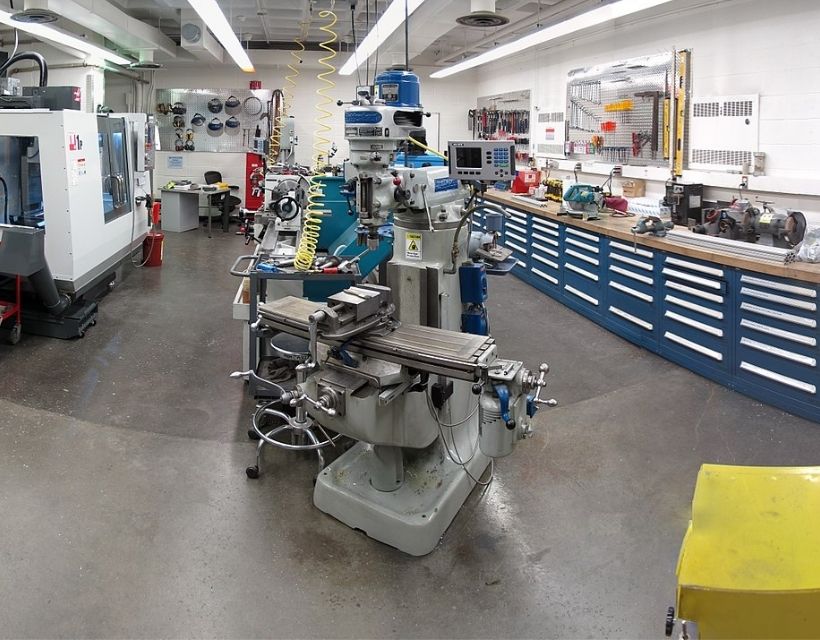
Learning Takt Time at Thales
A former VP of Operations from Thales tells Catherine Chabiron how he and his team turned around their department by committing to lean thinking and focusing on people development every day.
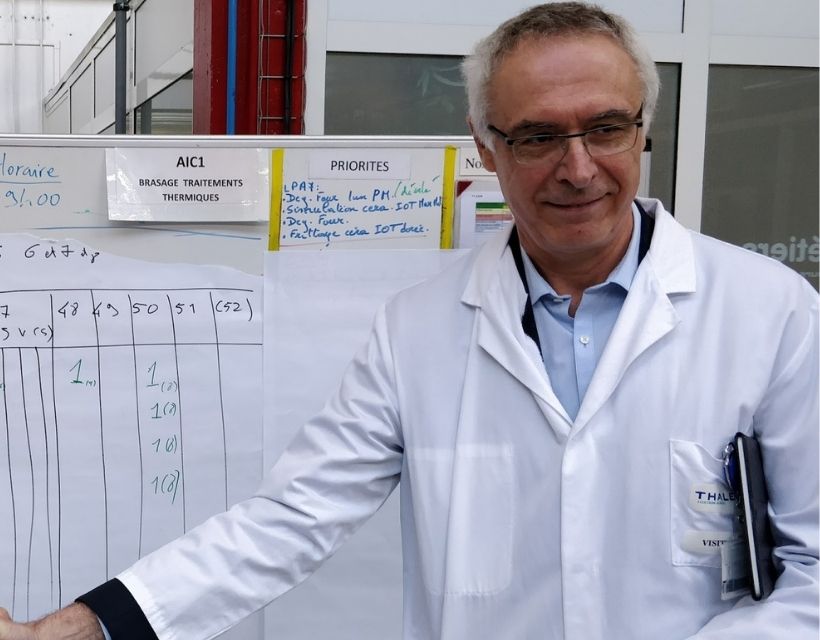
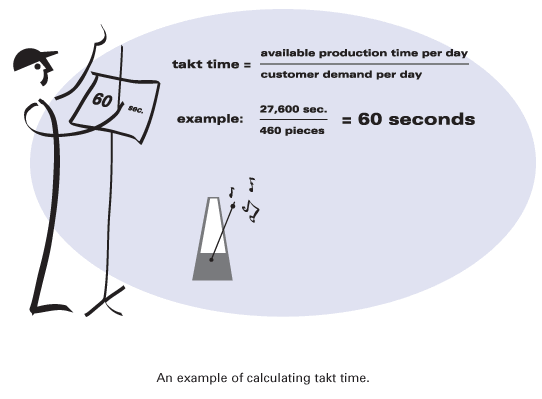