As this series continues to explore the implications and dynamic of “coaching” in a business environment, Bryant Sanders models the mindset and techniques for coaching work improvement to develop people. Bryant draws on 26 years Toyota experience to facilitate his coaching techniques with a team in the field leading to a dramatic improvement in the work. He walks us through the story from deciding where to focus, to earning the team’s trust, facilitating reflection solidifying the what and the why and then leveraging one another’s strengths to upskill the team and eliminate difficulty and waste in the work. An excellent study in masterful coaching on the floor where the work happens.
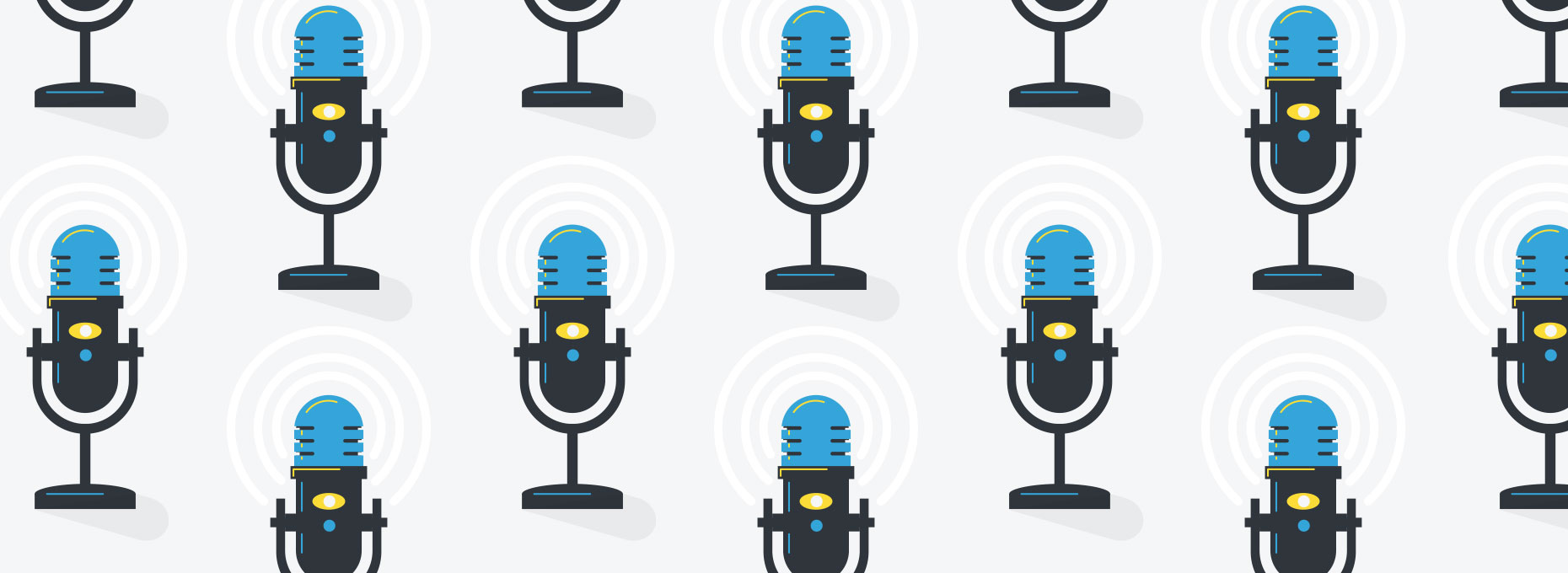
Operations
32. Coachable: A Model Story, Coaching Work Improvement
By Bryant Sanders
January 27, 2020
An excellent study in masterful coaching on the floor where the work happens.
Written by:
About Bryant Sanders
Bryant, a recent retiree from Toyota Motor North America (TMNA), has 25 years of experience in accessory development, supplier development, quality, logistics, production operations, and Toyota Production System (TPS) deployment. While at TMNA and working with the Toyota Production System Support Center and Operations Management Development Division, he learned firsthand the importance of focusing on people as the center of TPS’s management philosophy and technical practices.
As a coach and manufacturing leader, Bryant focuses on creating and managing resource strategies to launch new operations and products while achieving operational excellence. Through this work and coaching, he helps them better understand the work processes they oversee and adopt the mindset and behaviors that help them more effectively — and respectfully — lead work teams to practice continuous improvement that helps achieve organizational objectives.
Bryant has experience in teaching and helping organizations apply TPS principles in various industries, including but not limited to manufacturing, healthcare, and construction, achieving meaningful results to ensure customer satisfaction, cost reductions, and human capability development.
In addition to being a lean coach, he is an adjunct instructor of Supply Chain Management and Six Sigma Quality Control at Cincinnati State Technical College.
Related
Operations
Multi-level Visualization: Engage Everyone in Problem-Solving to Achieve Business Results
Article by Michael Ballé
Operations
Article by Matthew Savas