In March 2013, Kevin Nolan and Dirk Bowman shared lessons from GE Appliance’s lean journey at LEI’s annual Lean Transformation Summit in Orlando. This article tells the story of the GE and LEI lean co-learning partnership, in which we discuss the work at GE Appliance Park in Louisville, Kentucky. Stay tuned as this story develops.
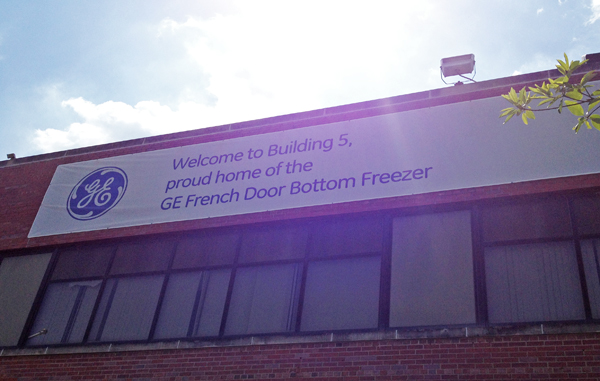
As policymakers and business leaders work to rebuild and reimagine a struggling U.S. economy, GE is not only at the center of the conversation about manufacturing, it is helping to drive it.
With operations in over 100 countries, roughly 300,000 employees worldwide, and annual revenue of 150 billion, GE is a household name and a staple of the U.S. economy. GE leads in such diverse markets as energy, healthcare, aerospace, transportation, business solutions, and home appliances. Appliance Park is GE’s largest appliance manufacturing operation. In an article for Harvard Business Review, CEO Jeffrey Immelt explains why in 2010 GE decided to invest $1 billion and make new product (mostly water heaters, washer/dryers, dishwashers, and refrigerators) in Louisville for the first time in over 15 years, creating approximately 3,000 U.S. jobs.
The goal has never been to apply lean tools here and there, essentially fire-fighting. From the beginning, it has been to seed and grow a new way of thinking across the entire organization.
GE saw several important business advantages to making new product at home again, what people are calling “insourcing”, “re-shoring”, or “onshoring”. In addition to creating more jobs, this would allow GE to avoid rising international shipping rates and material costs and gain more control of a global supply chain. Plus, making product off-shore meant separating design and development. To lead on creativity, it was essential for these teams be in the same place, working closely together. Insourcing may not result in immediate financial gain, but the long-term benefits can be substantial. [Read more about GE’s decision to bring jobs back to Appliance Park in The Atlantic]
Immelt is committed to helping bring about a new era in American manufacturing. “People talk about the Darwinian nature of markets,” he writes. “They say that America has undergone a natural evolution from farming to manufacturing to services… But nothing is predestined or inevitable about the industrial decline of the United States.” China’s performance in the global marketplace, for instance, shouldn’t discourage us, it should inspire us. Manufacturing may be changing, but it isn’t going away and it is still a significant component of America’s infrastructure.
So with GE Appliances building new products again (known as their “Mission 1” programs), why not build them in the most effective way possible? For GE, now is the time to invest in people, learn better production methods, and spread those methods throughout the organization. This is a chance for GE to set itself apart from its competitors, not only through new products, but through the creation of new and improved production and management systems (and lean leaders who think systematically). Immelt doesn’t just want to improve GE’s business, he wants to change the way the organization functions altogether.
This is where the GE and LEI partnership story begins. In the spring of 2011, when GE approached LEI, they were clear about their business need: could LEI help GE build a radically new management system at Appliance Park, one that would support new production and product development systems?
GE has a long history with continuous improvement, so most lean practices weren’t anything new. What’s new is GE’s attempt to practice lean thinking systematically while working with a brand new workforce and building brand new products on an aggressive schedule. GE Appliances has already launched eight new Mission 1 products. They are in the middle of four now. It’s an exciting and noble effort, and an extremely ambitious one.
Rich Calvaruso (GE Appliance Lean Leader), Bill McDonogh (HR Lean Transformation Leader), and Kevin Nolan (VP of Technology) all believe it can and must be done. They have the strong support of GE Appliance CEO Chip Blankenship. Together this team has been in the process of training employees in “GE-APS” (the GE Appliance Performance System), a system based on Toyota Production System principles, but utilized to meet the business needs of GE Appliances. LEI is helping GE do this through coaching and by developing people’s capability for continuous improvement. The goal has never been to apply lean tools here and there, essentially fire-fighting. From the beginning, it has been to seed and grow a new way of thinking across the entire organization.
With this larger goal in mind, here is where GE and LEI have focused their attention:
Developing Lean Leaders
GE Appliances is intent on developing a new management system to support its new product development and production processes. This means developing problem-solvers and leaders who act like coaches, helping others solve problems more effectively. LEI’s John Shook, Mark Reich, and Margie Hagene have provided executive coaching and team leader coaching, explaining lean principles and helping them think about what a new management system will mean for GE Appliances as a whole. On GE’s side, Rich Calvaruso and Bill McDonogh are working to spread lean thinking across all Mission 1s and train people in GE-APS.
Improving the New Product Development Process
By applying lean thinking to the NPI (New Product Introduction) process, GE Appliances teams are moving from what were essentially disconnected silos (with competing goals and metrics) to one, integrated team with one goal. This one team shares the same metrics (quality, time, service, cost) and is aware of all aspects of product development from the beginning. Last summer, team members across all Mission 1s gathered at GE Appliances’ training center to discuss and improve the NPI process on the whole, from design to manufacturing to supplier relations to delivery. Together they worked to identify problems and gaps, decide potential countermeasures, and determine ownership and follow through. LEI is assisting in a deep reflection process, to ensure that essential learning is captured now that the first new products have launched. Teams continue to work with management to test countermeasures, check and adjust.
Shop-floor Operations Improvement and Team Member Training
From the beginning, GE recognized that its new production and management systems would have to be actualized on the plant floor in direct production operations. LEI, with lean coaches Scott Borg, Noel Jarin, and Javier Sanchez, have assisted team leaders and frontline workers in making practical improvements in operations, focusing primarily on GE’s new refrigerator line. Teams have improved output in final assembly, allowing for the introduction of mixed model production. This has required a major redesign of work stations as well as systematic training in standardized work. LEI is currently helping the refrigerator team transform from a push to a pull system of production, from final assembly upstream to foaming, sub-assembly, stamping, and molding.
Organizational Strategy
GE is augmenting its traditional management systems with a strategy alignment process, maintained through PDCA (hoshin kanri). GE Appliances’ Roper operations in Georgia (another location in the process of building new products using a new workforce), is experimenting with a new strategy planning process. LEI will support these and other efforts to improve organizational strategy through training and coaching.
Learning Through Problem-Solving and Reflection
In spring 2011, GE Appliances established a cross-functional team called the “Little Big Room” (since this team was smaller than the “big rooms” of the Mission 1 teams) and studied exemplary companies such as Herman Miller and Autoliv to define the management behaviors and cultural principles required to transition to a lean enterprise. This work continues. LEI has assisted through advising on management system design, executive and team leader coaching, structured reflection processes, and problem-solving training. Key reflections on launches and on the NPI process as a whole are shared with top management. GE team members use reflection to become better problem-solvers and to open up new lines of communication at all levels, in all directions.
It’s all important work, but the GE Appliances team feels they have just begun. It’s one thing to understand lean principles and tools, or develop a lean production line or process, but how do you develop people to regularly practice problem-solving based on the scientific method (Plan, Do, Check, Act)? When a problem occurs, how do you address it and still keep the work flowing? How do you sustain progress when new managers or teams are introduced? How do you transfer learning across the organization? How do you help people become comfortable talking about problems and raising issues and acting their way to a new way of thinking?
These are some of the questions GE Appliances and LEI have been addressing since joining forces in 2011. In the words of LEI COO John O’Donnell, “Finding answers to these questions are key to developing production and management systems that will result in products that can be competitively built in America and provide real value to customers.”
As Charles Fishman says in The Atlantic, “The manufacturing renaissance now under way won’t solve the jobs crisis by itself, but it could broaden the economy, and help reclaim opportunities—and skills—that have been lost across the past decade or more.” It’s no easy task, but it has been done before. Proponents of lean thinking and practice have proven that these methods work. [Read about how LEI’s John Shook helped transform NUMMI, a GM and Toyota joint venture auto manufacturing plant, in the 1980s].
In the coming months, we’ll continue to share stories about GE Appliances’ lean transformation efforts.