LEI led a lean learning tour rooted in Michigan and Indiana, a place locals call “Michiana.” In this Post, LEI’s Josh Howell, a native Hoosier, explains the goals and underlying thinking behind this learning experience.
Q: Can you share some of the thinking behind the tour, Josh?
A: The idea behind the U.S. Lean Leadership Learning Tour is to spend a week exploring the journey and the process of Lean Transformation. We’ll frame that up at the start of the week, using LEI’s Lean Transformation Framework (LTF), and spend the week exploring various “case studies.” Not in a presentation sense, but in a tactile, gemba-based way, asking the LTF’s five questions at each stop. We will ask: What did we learn about this company’s stated purpose? What problems are they trying to solve, and how are they going about that? What are their unique capabilities, such as problem-solving? And then how are they managing that process at various intervals? Annual, monthly, weekly, daily, whatever. And more critically, we want to explore their underlying culture or the fundamental thinking that guides their actions.
So on day one, we will convene the group in Ann Arbor, Michigan, in the afternoon. On the first day, we aim to frame things up and orient the group around the transformation process, not only the result. In other words, we aren’t visiting perfect companies and saying, “This one’s perfect; emulate it. Instead, it’s to say: “These organizations are at whatever place they are in their transformation journey. Let’s experience that together and talk about how they got there, where they’re headed, and how.”
When I think about the idea of “all lean is local,” I think about the fundamental entry point question any lean thinker in any situation asks: “What’s the problem to solve…here…and now?” And if we start with that question, we’re already thinking locally.
Then on the first day of the actual tour, we’re going to go to two companies. First, we’re going to go to Zingerman’s Mail Order for a visit led by its managing partner, Tom Root, who is kind of a lean zealot, and then to Menlo Innovations to spend time with its founder, Rich Sheridan, and his team. There’s so much to see there, exploring their stated culture of joy. Rich has given many talks on how they operate, and we will witness it first-hand.
Zingerman’s is incredible. With Tom at the helm, they have developed a complete lean system that begins with the order-taking process. So, whether that order comes in online or through a phone call or a sales rep, they have an amazing visual display in their call center. This display shows a variety of information: how many calls are coming in, the sales results, who’s talking to who and how those conversations are going, and where there might be capacity. There’s a team leader in the salesroom who deploys calls when there might be capacity and also helps team members, through a kind of “kamishibai,” get tasks done during downtimes, which they inevitably have. It’s a really impressive, visually managed, highly productive, value-added sales operation.
Then we’ll go into the fulfillment center, where products are packaged and replenished based on kanban. The operation is set to a handful of different tasks, which dictate line flow, the number of resources deployed, and so on, to ensure that they ship the necessary quantity on time and with good quality. Also, Tom built a fair amount of technology into the process, which he created from scratch. So it’s an excellent example of technology, automation, data processing, and built-in support of the teams, not in a way that creates burden but in a way that relieves burden.
Tom’s been expanding lean into all aspects of that business, including marrying lean thinking up with Open Book Management, a practice for which they are quite well known. They even apply lean thinking to their hiring process, which is super challenging given the seasonality of their business, spiking in December before the holidays!
On Wednesday, we will have Sensei Jeff Smith take us through a simulation-based learning experience deeply rooted in TPS, diving into the fundamentals of work improvement, i.e., lean transformation. Jeff will quickly take the group through the transformation process, demonstrating the shift from a traditional push manufacturing system to one based on a pull system, breaking down the transformation process along the way.
Then, on Wednesday night, we’ll take a three-hour drive to northern Indiana to visit the Aluminum Trailer Company (ATC) on Thursday. ATC is a standard and customized trailer engineering and manufacturing company. They have two factories across the street from one another: one that makes their standard products — high volume with low variety. And the other, their high-variety, low-volume factory. So we’ll see how lean has come to life on the production side of things in two very different factory settings. The ATC leaders and team have not just focused on production but built lean into the entire business architecture — supporting business functions like finance and accounting. A complete lean business system. Cool!
Then on Friday, we’ll ask everybody to turn their focus toward their own situation. We will lead them through an exercise that will prepare them to apply their learning. In other words, to learn by doing. What can they bring back to their individual or organizational transformation that can give it a boost?
Q: How are they going to think and act differently as a result of observing these companies and participating in these exercises?
The promise is not to show you perfect lean examples to copy and paste. The promise is more about studying examples of organizations undergoing lean transformation, trying to learn from their experience …
A: One answer would be that it will depend entirely on where they and their organization stand today along their transformational path. But I guess the better answer is that we’re all going to spend time learning to think through individual and organizational transformation. So, for example, we’ll tackle questions such as: What are the components of organizational transformation? What are the key questions to regularly address to be successful along that path?
We’ll use the LTF to help equip folks with a thinking construct to more effectively lead their organization, from where they are today to where they need to be tomorrow. Whatever level you might be in your organization, we want to help broaden your perspective on how you think about where you are, where you want to go, and how you’re going to get there. And then send you back to your business well equipped to put that thinking into practice, solving today’s critical business problems. The promise is not to show you perfect lean examples to copy and paste. The promise is more about studying examples of organizations undergoing lean transformation, trying to learn from their experience, and reflecting on that — and then reflecting on our own situations to say, okay, what might we bolster, what might we stop doing, what might we just tweak, modify, in our approach that will help accelerate our journey from here to better.
Q: It appears that there are principles of lean learning embedded in these tours; are you and the folks at LEI doing experiments to teach lean in different ways?
A: Yeah, we are. We’re reticent to offer learning tours that are traditional industrial tourism — like let’s look at the blinking lights, andon boards, and standardized worksheets. We will see those things for sure, but we really want to frame it in terms of the underlying thinking and the journey, I guess, for lack of a better word. The process for improving business outcomes — improving results that customers deeply care about.
So this tour offers lots of learn-by-doing, lots of going-to-see, and lots of interactions with folks doing the work. To hear from them directly and to listen to them speak frankly. We are also coming at this with a fun little question: How can I up my improvement game?
Q: It’s interesting. You’re doing three tours, and only one of them is traditional manufacturing. Does having a diversity of companies and industries enable you to help people see common patterns, ways of thinking, or approaches?
A: That’s right. The commonality is that each of these organizations had a problem to solve that led them to experiment. Or the commonality can be the questions they’ve asked along the way versus the commonality being, oh, I don’t know, that all of them use kanban or standardized work.
I think we’re going to see a lot of diversity even in workplaces where there might be similar operations. For example, Zingerman’s and ATC both have customer call centers — more or less the same function. But there are also differences: one business is massively seasonal in the form of a food-based mail-order business, while the other is less seasonal. Learning how to explore those in a consistent way that participants can learn from is where we’re relying heavily on the lean transformation framework to be a lens through which we’ll study these different examples.
Q: Another way of framing that thought is to say that “all lean is local.” I’m not saying this because you are a Hoosier yourself. But saying that, it feels like the thinking behind this tour (and beyond) frames lean as a set of universal principles that take root, as it were, in the vernacular of local business.
A: When I think about the idea of “all lean is local,” I think about the fundamental entry point question any Lean Thinker in any situation asks: “What’s the problem to solve…here…and now?” And if we start with that question, then we already think locally. Right? It’s not a question that leads me into a broad-based exploration; it’s a question that forces me to reckon with the place where I’m currently standing and with the people there and the work they’re doing — the problems they might be trying to solve. So in that sense, I think lean is, by its very nature, about local practice and local thinking.
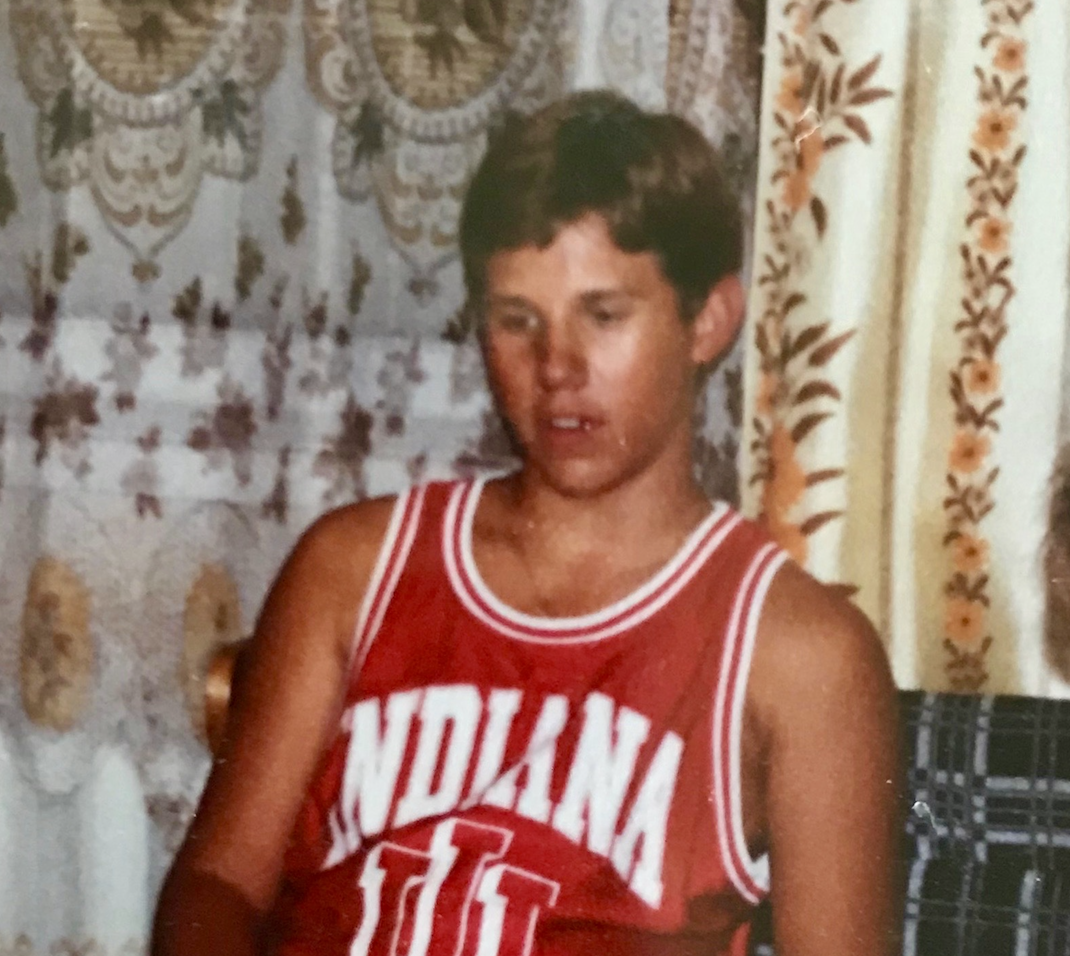
And so yeah, for me, it’s exciting to return to where I was born and raised, to where I went to college. I’m kind of tickled by having the opportunity to return home 15 years after leaving to begin my professional life. Those 15 years bookend my entire lean learning, my personal lean transformation. This tour is an opportunity to reflect on how my worldview has changed. Let’s just say that I grew up in South Bend with more of a solution mindset than a problem-solving mindset. And I believe this shift has been key to my personal transformation.
Editor’s Note: This Lean Post is an updated version of an article published on April 19, 2019, one of the most popular posts about this vital lean practice.