When an operations director of a large energy company asked our continuous improvement team to help his staff with their operational discipline, the first question we asked was “What do you want to see as a result of this work?” His response was that he didn’t want to get to work in the morning and find the plant not operating to specifications, with no documentation of the issues or the responses. We laid out a vision for him that involved his team looking at the important things frequently and responding to variations in a standardized way, all with an eye towards improvement. His response was, “I want that!”
Reviewing the objective, it was clear to us that implementing standard work (SW) with leader standard work (LSW) to reinforce it was the way to go. It sounded easy, but, as we were to find out, there are always challenges and pitfalls when implementing this type of change. Here are the four main pitfalls we encountered and, upon reflection, how we could have navigated them.
Pitfall 1: Adding new tasks without considering existing workload
The first issue we had was adding LSW tasks to the already-overloaded front-line supervisors. With all their meetings and reports to do they had little time to complete a field tour with an operator every shift.
How can you avoid this pitfall? Before you build a LSW program you need to identify the standard work for all positions. This is not about polling everyone or completing a “Day-in-the-Life” study to identify and standardize the existing tasks. If you just standardize what everyone is already doing and then add on new LSW, the employees will be overwhelmed and your plan is much more likely to fail. You need to make room in their existing workloads first.
Try an exercise whereby you categorize everyone’s tasks across all roles into one of the following categories:
- Value added
- Business nonvalue added
- Nonvalue added
Have everyone write down individual tasks on small pieces of paper. Then, with the taskholders in the room with you, place each task into one of the above categories. At the end, keep the value added, keep or delegate the business non-value added, and delete the non-value added tasks. We record the results in a chart like this:
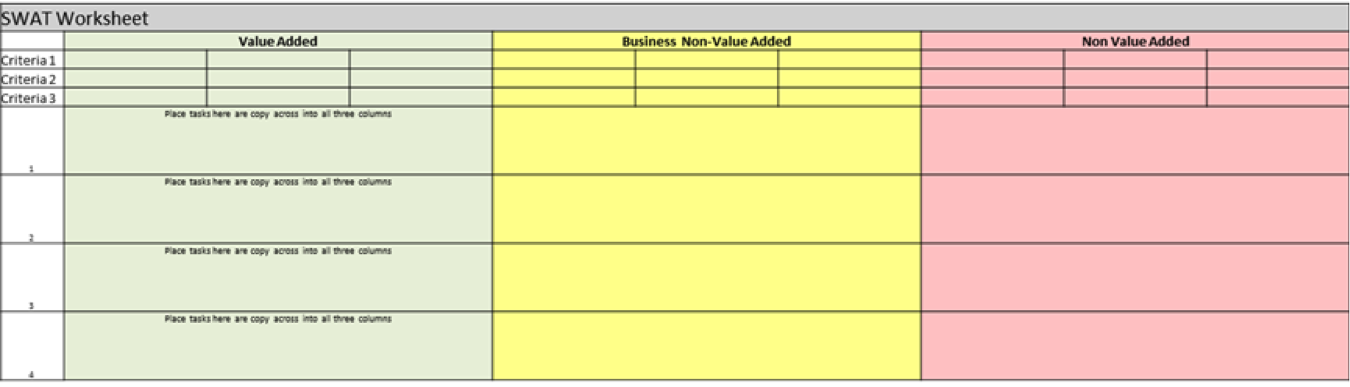
You may be surprised at the results you get from this exercise. In this case, the director realized that his supervisors were not aligned with his priorities. He wanted them out in the field ensuring that the operators were performing their tasks safely. In reality, this wasn’t even one of the tasks that the supervisors identified. Ultimately this realization led to much-improved alignment between the director and his supervisors.
The key here is to seek participation from every role. Had we completed this step for all roles up front it would have helped us get immediate buy-in and speed up the change management process.
Pitfall 2: Implementing LSW without SW (and vice versa)
LSW does not have to be overly complicated.> At its most basic, LSW is simply standard work that supports the work of others. Everyone, including leaders, has standard work – value-adding tasks that support the overall objectives. It is important to distinguish between LSW and SW while also realizing that you cannot have one without the other. LSW without SW is a waste of effort as the support will be unfocused (and sometimes unwanted). SW without LSW to reinforce it will last no longer than it takes you to drive out of the parking lot. Build SW first and then add LSW to support and reinforce it.
Pitfall 3: No improvement process for SW
Early into our initial implementation, a front-line engineer came to us and showed us an outdated procedure that could be made more efficient. We were very excited by this autonomous improvement but it brought up a question: what was the process for making improvements to the standard work? This happens when there is too much focus on standards and not enough on continuous improvement. Having too many standards without a mechanism to improve them will slow productivity and significantly reduce the buy-in for changes. Standards are good as they allow you to stabilize; however, not allowing them to improve is a recipe for disaster.
Part of any good continuous improvement program is the investigation of unexpected results – both good and bad. The former may sound strange – how many people or organizations put as much rigor into investigating over-achievements as under-achievements? Not many, but instances where you beat expectations can be more fun to investigate, teach you just as much or more, and often result in a new “best way.”
Pitfall 4: Rewarding the Wrong Behaviours
The last crucial piece for long-term success is to make sure that you reward the right behaviours. There is a temptation to reward the best “firefighters” on the team, and this just ensures that you’ll always have fires to put out. For example, at one plant there was a supervisor, widely recognized as one of the best in the company for his ability to fix any problem on his own But when he left, his crew went from one of the best to one of the most challenging – they didn’t know how to fix anything for themselves without their fix-all supervisor. And, because the senior leaders rewarded the supervisor for these behaviours and had him train other supervisors to follow his lead, the cycle continued and spread.
To be fair to him, he thought that he was doing the right thing, as the proper process was never instilled. But once the “best way” is in place, senior leaders need to recognize and reward the people who follow it, along with finding new ways to continuously improve it.
We learned a lot during our implementation of standard and leader standard work. We have seen steady improvement in the consistency and reliability of our key performance indicators and in our bottom line results. The director gets the information he needs and variations are caught quickly and acted upon correctly.
Is it perfect? No, but it’s created a path to follow and a process for improvement. As for us, our next path will have fewer pitfalls.
¡Muchas gracias por esta información! Me ha sido muy útil en el proceso de aprender el tema de LSW. Hasta el momento, no tenía contemplado el tema de SW y ahora me siento un poco preocupada, ya que estamos por iniciar la implementación de LSW en la organización donde trabajo, pero no trabajamos nada del SW. Si no funciona, entonces ya sabremos que hacer.