A few months ago, we spent several days together at Tyson’s company, O.C. Tanner, which is renowned for its high levels of continuous improvement activities and employee engagement. Lean practitioners visit the company (Josh in this case) from far and wide to learn about its “special sauce.”
One ingredient in the company’s recipe—standardization—became a central topic of our co-learning activity. Interestingly, perhaps counterintuitively, O.C. Tanner’s leaders use standardization to build ownership across diverse teams and enhance performance for a variety of customers. To fulfill this purpose, they avoid the temptation of using a kind of standardization—what we’ll call commonization—to make things easier for themselves.
O.C. Tanner’s business is employee recognition and rewards. One might assume, therefore, that the organization has a healthy culture of its own. Contrary to the adage “the cobbler’s kids have no shoes,” this assumption holds true for O.C. Tanner. Josh had the privilege of joining a well-attended and well-run 25-year anniversary celebration during his visit. Tyson confirmed that such events are commonplace.
Many companies, whether lean thinking and practice is present or not, are disciplined when it comes to employee recognition. Yet few companies have, much less sustain, cultures of highly engaged people steadily making things better through conscious continuous improvement. O.C. Tanner must be doing something different. We believe a key factor is their emphasis on standardization over commonization.
We define these two terms distinctly. Standardization is the best-known way to do something in a specific context, figured out by those doing the work. Commonization, on the other hand, is the best-known way to do something universally, as decided by a central authority. With standardization, people control their own work; with commonization, “others” control it. In our experience, lean practitioners often say standardization when commonization would be more accurate. (For more, check out John Shook’s 3-part article 5 Missing Pieces in Your Standardized Work.)
O.C. Tanner is organized into mini factories, typically u-shaped cells where small teams manufacture various products using similar materials. As described in the LEI workbook Creating Continuous Flow, u-shaped cells enhance workflow and foster teamwork. Within these cells, each team employs a visual management system that shows their goals and guides their work. Upon close inspection, while there are commonalities, each mini factory’s system is in fact unique.
While it is familiar to Tyson, each team working and managing in their own way caught Josh’s attention. He learned that O.C. Tanner’s leaders set standards to clarify what is expected in terms of safety and quality, while teams use standardization to define how they will meet those expectations. In other words, global standards beget local self-management.
For example, the company has certain standards for inventory. Yet teams have the autonomy to experiment with different techniques for material flow, like the use of kanban or kitting. Similarly, every visual board displays a common set of KPIs deemed critical for meeting customer expectations and ensuring profitability. But each team is free to choose its own methods to achieve its measurable goals.
According to Tyson, this approach is meant to show genuine respect for each team member’s experience and capability. Rather than imposing top-down commonization, leaders foster a learning environment by encouraging people to question every detail. This keeps the methods used (i.e., process) in balance with the users’ understanding and skills (i.e., capability), enabling sustainment.
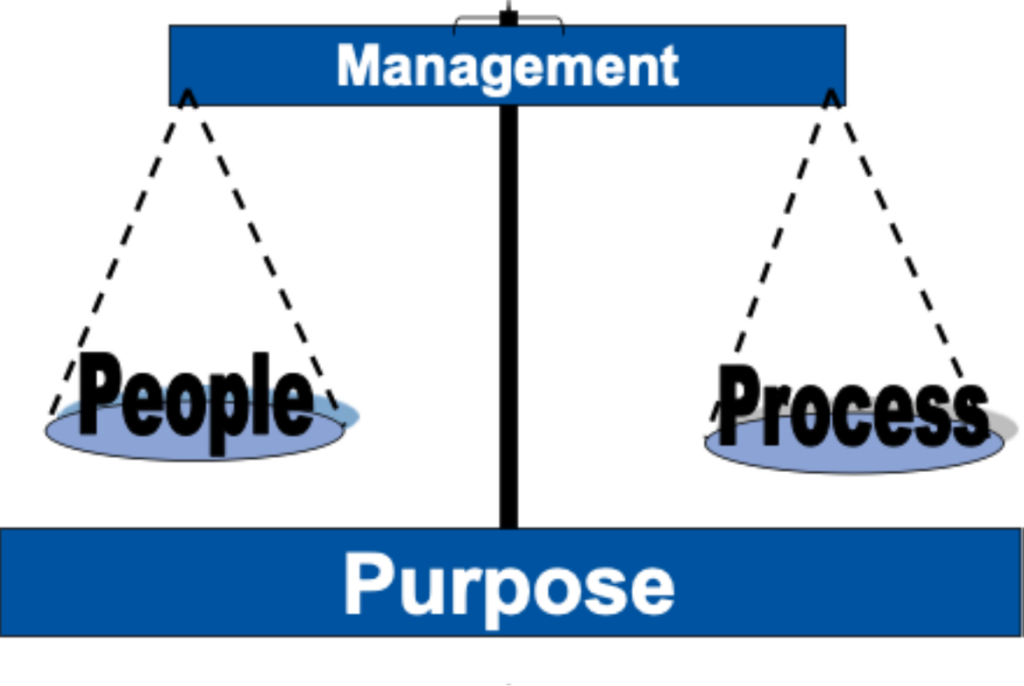
At O.C. Tanner, team members can even challenge bedrock lean thinking and principles such as single-piece flow. Those who doubt the wisdom of reducing batch sizes, for instance, can experiment to see firsthand the impact on quality, productivity, etc. “Lived experimentation” defines the company’s culture.
This approach is like a “pull system” for improvement. Ideas spread naturally person-to person based on their perceived needs versus forcefully by leadership edict. Leaders encourage peer-to-peer sharing by regularly visiting the gemba (workplace), engaging with team members, and connecting people to exchange relevant ideas. An annual improvement fair also helps teams showcase their innovations and learn from each other, highlighting their lean thinking to one another.
So, why do so many companies choose commonization over standardization? We believe this is because (uplevel) leaders, perhaps unintentionally, put their needs over those of their (downstream) customers. Lean management is difficult. Commonization—creating sameness—would seem to simplify it. But what we see in practice is the opposite.
First, commonization may overlook customer (product) and process variability, creating its own set of issues that can flummox managers and workers alike. Second, because commonization gives management ownership of the work, such issues can erode management’s credibility. Third, because commonization is centrally controlled, the central authority bottlenecks problem-solving and improvement. And finally, an imbalance emerges between method and knowhow (process and people), jeopardizing sustainment.
In today’s ever-changing business environment, continuous improvement is essential. By valuing standardization over commonization, leaders can build ownership in teams for their own work as required for improvement to be continuous (versus episodic). We encourage all leaders to embrace this approach to standardization. While it does require time and effort, in the end it engages everyone in making things better, creating sustainably high-performing organizations.
Sincerely,
Josh Howell and Tyson Heaton
P.S. If you would like to visit O.C. Tanner, or if you’re just interested in discussing or debating the role of traditional lean tools such as standardized work going forward, you can join us at the next Future of People at Work Symposium. This year’s Symposium will be held at O.C. Tanner on June 26 and 27, 2025. Thanks to Gary Peterson, the company’s EVP of Supply Chain and Production, for agreeing to host. Click here to learn more and register.
Future of People at Work
This unique event brings together practitioners, leaders, and thought pioneers to shape the future of work through collaborative problem-solving and shared learning.
I work for a large multi-specialty medical group. We are about to start standard work for the Call Back, Vitals, Care Gap Closure and Discharge of patients from our office clinics. In healthcare there are many regulations, guidelines and evidence based practices that are the standards within which these process need to work. Hence, our standard work fits the definition of Commonization. We have and are promoting the idea that the current one best way is not meant to be static, it should be improved by the people performing the work. There a also many opportunities for problem solving at the frontline which we want to engage frontline staff in solving. The standards don’t change that frequently but as long as we do fulfill them, we can improve how we do it. What are your thoughts about standardization vs commonization in a highly regulated healthcare environment? What advice might you have for us in how we position standard work for our staff so that it does help to create a continuous improvement and problem solving culture? Thank you.