- In its essence, value-stream mapping is the same at every level. Mappers try to capture on one sheet of A3-sized paper (11” x 17”) a two-dimensional representation of the material and information flows of the value stream. The objective is to render in simple form that which seems so complex and confusing in real life, so that we can change our focal plane from narrow operation efficiency to total value-stream optimization. Just as with manufacturing facility mapping (as described in Learning To See), we first draw a map of each step in the current state from which we devise a future state that we then implement right away.
- A map for a support function looks much the same as a map for a manufacturing facility, with process boxes, data boxes, information flow arrows, and a timeline across the bottom. The biggest difference between support operation and plant mapping is in the distinction between information and material flow, which in manufacturing is very clear. Furthermore, simply drawing the map with these distinctions will almost always lead to numerous “Ah-Ha’s!” with critical questions almost jumping out at the plant mappers. Ideas for countermeasures then flow quite easily. This is especially true since we can articulate quite clearly the characteristics of a lean value stream for manufacturing operations. First-time mappers in the plant usually become excited and inspired from the new found clarity gained from the plant-level map.
- All these material and information flow issues change when mappers leave the plant floor to map support or administrative operations. First, a clear distinction between “material” (or process) flow and information flow often cannot be made; the information moves with the material. (Often, extensive discussion is required to even determine what is the material that should be mapped!) When the information and material move together, the magic of the two-dimensional visual representation of the value-stream map is lost. On the surface, the map becomes little more than a glorified flow chart, or “process map.” The relevant factor is, however, just as it is with any tool, the purpose or intent one brings to the use of the tool. Even without the clear information flow arrows descending from above (as with manufacturing facility mapping), creative use of the data boxes, timeline and future-state questions can still lead a mapping team to a new focal plane, new countermeasures, and a viable future state.
- The lack of distinction between material and information flows and the fact that the information travels with the work means that it can be very difficult to even draw the top half of the map, which is the information flow. In the plant, mappers draw a “production control” or “scheduling” box, from which production instructions flow to each operation, attempting to tell each operation what to do and when to do it. The questions used to identify those information flows range from asking operators the simple question, “How do you know what to do next?” to asking information system specialists for historical customer order data to analyze. For support functions, even if the information and work seem to flow together, mappers should at least try to go through the same process and ask the same questions. This will be very important when working through the future state. Even in the office, work is being performed for some customer. Who is that customer, what are his or her needs, with what timing does he or she require the work? With such questions, administrative or support function mappers can try to draw the information flow separately, even if the information is not literally coming from a central scheduling function
- As with drawing the information flow, support operation mappers should try to go through all the future-state questions. Some of the questions may not seem to fit well with some types of work, but the questions provide a good framework for discussion to better understand the issues and what needs to be done to envision and implement a lean Future State:
- Takt Time. Most mappers new to the mapping of support functions skip over takt time, thinking that it doesn’t apply or is simply too difficult to determine. This is a big mistake. Always spend time trying to determine a viable takt time. Even if the end conclusion is one that leaves some remaining gray area, the discussion and even tentative conclusion are critical.
- Flow. Why does the work sit in queue? Why can’t it flow from one processing step to the next? This tends to be the biggest factor in long lead times in office work — the waste of waiting, as work sits in someone’s inbasket.
- Pull. This is why it’s important to try to map the information flow. Questions to ask include, “Who is asking for this work?” When do they require it? How frequently do they require it?” Then the mapping team can try to address the question, “Is there any way a direct pull system can be applied to this process?” If you can find a way, then you’ll find great success!
- At what single point do you trigger production? How much work to release and take away? How to level? These questions all relate to determining ways to somehow rationalize the information flow, or clarify the process of initiating the work. In particular, finding ways to level the work (heijunka) can be a game breaker in office work. For that, you’ll need to find a way to calculate the takt time for the work.
- Process Kaizen. The question of what process kaizen is needed requires detailed knowledge of the work content. That leads us to the next item, data boxes.
- The data box is critical in any map (and too often left blank!), and in an office environment will often represent the biggest difference between value-stream mapping and other mapping tools (flow charts, process mapping). The team will need to spend time determining what data are important. In many cases, it is the analysis of this data that will lead to most of the important future-state improvements. The determination of what data to include in the data box will depend on what questions about your value stream you are trying to answer. Typical data for plant-level mapping include cycle time and changeover time. At the macro level, important data points tend to be EPEI (every product every interval), shipment performance (premium ships), and total inventory in raw material, WIP, and finished goods. What data are truly important for your support operation?
- Ideal State. Plant-level current-state maps tend to expose a tremendous number of improvements available for immediate benefit, easily focusing attention on a future state that can be implemented quickly. Support or administrative current states are often so confused, convoluted and on the surface even nonsensical that the team may want to jump to ideal-state considerations. A word of caution here: it is often too easy to jump to solutions that sound great but are not implementable. Remember that each waste is there for a reason and we need to understand the reason so we can eliminate the root cause of the waste, at either the process or the system level.
- Metrics. The timeline will provide one of your key metrics. But, how important is time to the specific process you are mapping, and what other measures can you use? Costs are typically very hard to quantify in support operations, and much time, effort, and emotion can be expended debating it.
- The most important key to remember when improving a support function work flow is that all actions fall into one of three categories: 1. value-creating work, 2. nonvalue-creating work that is currently required, and 3. muda, waste or non-value creating work that can be eliminated immediately.
It is easy in the plant to determine (at least on the surface) whether an action creates value: the act of performing a spot weld is creating value (unless, of course, it is an unnecessary “processing muda” step, the most difficult type of muda to learn to see), while the act of discarding or reworking a bad spot weld is muda. But, in the office, where most support activities take place, everything falls into the difficult category of nonvalue-creating work (what Womack and Jones call “type one muda”). Yet, since all office activities fall outside of the first category — value-creating work — the challenge in the office becomes determining the difference between nonvaluecreating work and muda.
To use an example from the plant, all inspection operations are nonvalue-creating. But, redundant inspections are muda, while an inspection that is truly necessary to provide customers with what they want, is nonvalue-creating work. In the office, we need to determine which operations are truly wasteful (and could be eliminated today) and which operations are performing a necessary support function for the true value-creating operations that take place elsewhere, whether in the factory or in the laboratory. To make this determination, these two questions, asked in this order, are often helpful:- Does this action support a value-creating step performed either here or elsewhere?
- Can this action be improved or eliminated?
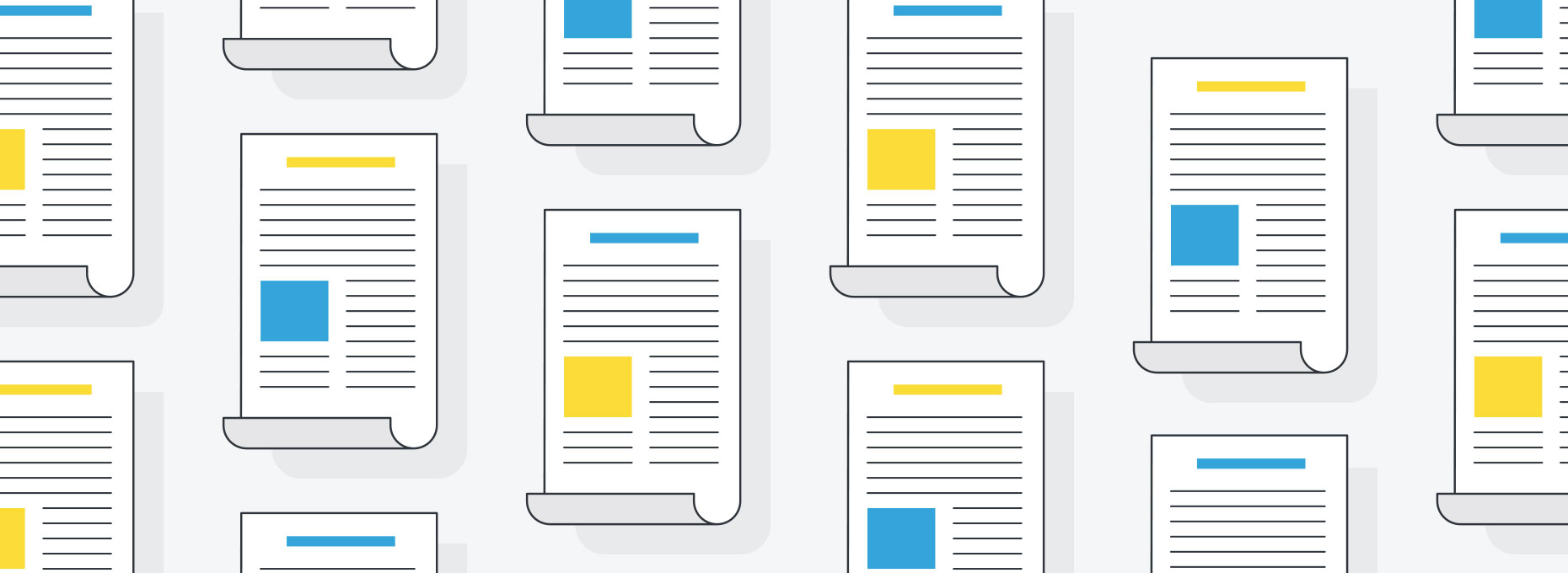
Administration & Support
Helpful Hints about Mapping off the Plant Floor in Support of Administrative Operations
Off the shop floor, the distinctions between material and information flows often blurs. Here are nine suggestions from LEI author John Shook for adapting the mapping tool.
Oh goodness … am I missing something? It seems the article ends without providing the two questions that must be asked in order when determining whether an activity is necessary or truly wasteful.
Good catch! This has been corrected.