Manufacturers, healthcare organizations, government agencies, and others gain powerful benefits through collaborative learning and networking in lean consortia. Consortium members trade improvement ideas and experiences, develop peer-to-peer connections with fellow lean practitioners, and share the costs of training and educational events. They also find shared understanding that lean is more than a set of tools and techniques; it’s about relationships and learning from others about better ways to improve customer-focused performance. Several lean consortium leaders share their “lessons learned” for launching and facilitating the organizations. Although their approaches vary, the vote is unanimous on this point: Don’t wait for the “perfect” organizational launch – get started!
Trading improvement ideas and learning with fellow lean practitioners, sharing costs for training programs, and networking through Special Interest Groups (SIGs) are benefits from lean consortium participation counted by Alissa Nichols, continuous improvement manager at Columbia Machine in Vancouver, WA. She’s a member of the Northwest High Performance Enterprise Consortium (NWHPEC) based in Portland, OR.
Columbia Machine employees launched a pilot suggestion/idea system in the machine shop, following a NWHPEC presentation by Ideas Are Free author Alan Robinson. Noting that “gaining a continuous improvement culture is on everybody’s radar screen,”Nichols also participates in a Toyota kata SIG. “You’re partnering with other companies that have started on the lean journey,”she said. “From the ideas that I’ve received, I’m still learning and having those ÔAha!’ moments.”
“You’re Not Alone”
Nichols’ experience reflects powerful reasons for joining – or starting – a lean consortium. Julie Simmons, NWHPEC executive director, cited several key benefits from these collaborative learning organizations:
- Learn and improve together
- Gain perspectives from other companies and industries
- Develop peer-to-peer relationships
- Share the costs of training and educational events.
“When you’re learning from others with similar experiences, you learn that you’re not alone in experiencing these challenges, whether you’re a CEO, a manager, director, or shop floor folks,”said Simmons. Members report practical learnings from educational events presentations as well as informal storytelling before and after the sessions.
NWHPEC membership is open to companies and organizations on a continuous improvement/lean journey, not to individuals or consulting companies. Members include manufacturers, distributors, government, retailers, and healthcare organizations. “You can apply some of the same lean concepts and tools in different organizations,”Simmons said. “We’ve learned that a process is a process.”
Every organization brings something to share with fellow consortium members. Members “give back”in various ways – hosting tours and other events, contributing ideas and expertise on selected topics, facilitating events, and distributing consortium materials.
Participation in events such as a presentation by Toyota Kata author Mike Rother clearly reflects whether the consortium hits the “What’s in it for me?”target. Event planning flexes based on attendee feedback — the “Check”element in Plan-Do-Check-Act (PDCA). NWHPEC programs evolved from training on lean tools several years ago to a focus on culture: how people behave and improve on a daily basis in problem exposure and problem solving. “We may branch out with an online member forum,”Simmons said. “We also continue to focus on fundamentals and coaching for improvement at all levels in organizations.”
Get the Flywheel Turning
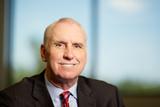
Lean consortium members gain shared understanding about generating long-term, continuing performance improvements, believes Jerry Bussell, founder and director emeritus of the Jacksonville Lean Consortium (JLC or LeanJax). “It helps to get the flywheel turning in organizations,”he said of the Florida group. “Lean is effective as a series of small projects in small bites — increments tied to larger goals. Continuous improvement is not episodic; it grows organically.”
Lean consortium members speed learning through networking, training and collaboration with lean leaders from various arenas – manufacturing, healthcare, government, and professional services. Training initiatives target practical application. JLC offers employee development certification programs and annual structured peer assessments (“Check”to drive “Act”). Another plus: Each new member partners with a mentor from another organization. “They share what they want to achieve during the coming year, gaining a trusted resource and motivation to ensure results,”Bussell said.
JLC provides basic lean education through its own lean leaders meetings and liaisons with the University of North Florida and Underwriters Laboratories. “We are redefining our role in the members’ lean journey,”said Joe Krall, finance manager. Lean certification, a lean mentoring program, and a recommended self-assessment process contribute to sustained lean progress.
Members benefit from non-traditional shared learning offerings. “We’ve realized that actually doing something during our meetings – focusing on problem solving, for example – helps our members work together to help each other improve and become more successful,”Bussell said. Added Krall, “Employee development gains are every bit as important as business gains. Participants learn from their peers how to approach a problem and expand problem-solving skills as they are exposed to a wider set of variables.”
JLC encourages members — approximately 40 companies and two hospitals — to ask for what they need as their challenges evolve. “Through the consortium, we help to facilitate deeper relationships and collaboration within organizations and between companies, including CEOs,”said Bussell. He believes that JLC’s integrated offerings — training, mentoring, assessment, certification and individual members — help members to serve the community better as they improve organizational performance.
LeanJax Consortium Guidelines
Member guidelines vary considerably among consortia. Although “what works best” depends on a group’s mission, goals, and other factors, consortium leaders agree on this point: Don’t wait for the “perfect” organizational launch – get started! The Jacksonville (FL) Lean Consortium (JLC, or LeanJax) shared its membership guidelines. The group’s general description: JLC represents a cross-section of enterprises whose mission recognizes the need and desire for each member to achieve world-class performance. JLC members range from small to Fortune 500 companies, industrial and other private industry enterprises, government agencies, and professionals. The JLC vision: Be the forum for its members to become more efficient and effective through networking and shared learning in continuous improvement and lean principles. Its mission: Be the forum for education and the exchange of information regarding ways to develop, implement, and improve processes, practices, and procedures in the southeastern portion of the United States through the implementation of lean thinking, methods, and tools. JLC expects members to participate by hosting consortium events, assisting other consortium members in their events, and including other members in their events. Incentives/rewards for hosting events may include discounted membership dues and admission to special JLC events or credits toward future training expenses. Members in good standing participate in at least one semi-annual JLC “Lean Kaizen Day,” vote at the annual meeting, refer at least one new member each year, and participate in JLC-sanctioned survey projects. JLC also encourages senior management commitment and participation in its events (as instructors/leaders when they have needed expertise), quick response to consortium surveys and requests for benchmarking data, and contributions of brief progress summaries and reports when requested for brochures or newsletters.
Building a Network for Your Lean Journey
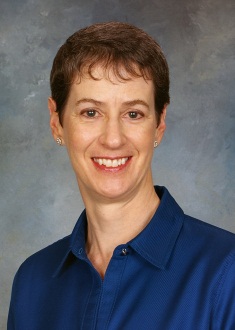
Passion for lean principles and for collaboratively mining great ideas power the member-driven Iowa Lean Consortium (ILC), according to Teresa Hay McMahon, president. With 34 organizational members and 22 individual members, the group serves all sectors in the economy, from manufacturing and healthcare to services, education, and government. “The consortium is about relationships and learning from experienced lean practitioners, not just learning about lean tools and implementing lean,”Hay McMahon said.
One of the group’s key values is building a network of folks who share a lean journey. “If we’re struggling with solving a problem, we help each other find places to benchmark and sometimes we blatantly copy ideas. We also provide access to training and information about lean concepts,”said ILC board member Gina Singer, continuous improvement manager, Pella Corporation in Pella, IA.
Manufacturers gain useful perspectives and counsel from lean practitioners in other fields through consortium-sponsored activities. For example, a Pella staffer co-facilitated a roundtable discussion with a leader from Mercy Medical Center. The ideas and concepts shared in this session resulted in the development of curriculum based on the book, Influencer : The Power to Change Anything, by Kerry Patterson, Joseph Grenny, David Maxfield, Ron McMillan, and Al Switzer. This curriculum is used in all Pella departments to help the team influence the creation of a problem-solving culture. “In addition to collaborating with Mercy Medical Center personnel, we have also implemented concepts from Wellmark and Rockwell Collins,”said Singer.
ILC encourages information sharing even among competitor organizations. “We ask host companies if they are comfortable having competitors attend their event, and respect their preferences,”Hay McMahon said.
The Iowa consortium keeps costs down by calling on members to host events and provide meeting facilitators and speakers. Although volunteer facilitation assistance can work well in a lean consortium startup, hiring a professional coordinator makes sense as program offerings expand, said Hay McMahon. “You can only work so long on a pure donation-of-time basis,”she said. ILC employs a virtual assistant to organize and promote events, update membership and recommended reading lists, and manage its website. Members check a calendar on the ILC website, tapping into team leader and other classes available only to members. Networking and collaboration with other groups such as the local Manufacturing Extension Partnership (MEP) and the Iowa Quality Center also boost members’ opportunities to trade lean “lessons learned.”
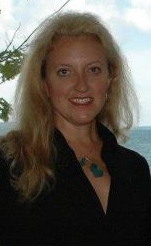
Collaborative Spirits
Passion for creating state-wide lean training opportunities and fostering Michigan’s growth ignite collaborative spirits in the Michigan Lean Consortium (MLC). “We are bringing together a community that is hungry for collaboration, communication, and involvement in our opportunities,”said Debra Levantrosser Setman, chair of the MLC board of directors.
“We are known for providing training opportunities for anyone in Michigan who is interested in learning more about lean principles and practices, and fostering growth in our state through collaborative efforts,”added Julianne Leigh, membership liaison on the MLC board of directors. “We encourage manufacturers, educators, banks, healthcare providers, and other groups to meet and learn how lean can apply to all these different industries.”
MLC started in 2008 as an individual member-based organization. Now it welcomes organizational memberships. “It’s so beneficial for a group to bring lean concepts to their organizations,”said Leigh. “We listen to their desires and needs, then plan related educational opportunities, extending the reach of the organization and benefiting surrounding communities.”
“We are evolving into an education-based lean consortium,”Levantrosser Setman continued. “We bring together organizations looking for training and also more practical, hands-on experiences.”MLC’s repertoire ranges from training courses on lean concepts to leadership panels, one-on-one sessions with authors and leaders in the lean world, and benchmarking opportunities where participants “walk the line”with lean practitioners. “Our members say we are affordable and accessible,”said Levantrosser Setman. “Our mission is not to raise a lot of funds through membership. It is to spread lean principles and share value.”
Some members join for lean education, others want to network and learn from fellow lean practitioners, while “improving Michigan”tops others’ wish lists. “We all rally around our passion for encouraging people to be a part of our lean improvement vision, and that can benefit the entire state,”Levantrosser Setman said. “As the excitement grows, it becomes an amazing, life-changing experience.”
The group’s evolution continues. “We are always looking for ways to improve the quality of our programs,”Levantrosser Setman said. “Yet lean learning is woven all the way through, for consistency in our messages.”Alliances with organizations such as Northwestern Michigan College in Traverse City, MI broaden MLC’s lean education and knowledge base. MLC also is working on expanded website resources, a lean certification process, extended geographical outreach, student chapters,and forging liaisons with communities and government offices that strive to do more with fewer resources.
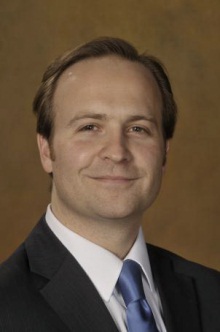
For example, dozens of MLC members volunteer their time and expertise to help the State of Michigan on a host of improvement projects. “We are advancing a culture of relentless positive action under a banner called Good Government, which will help our government run better, through customer-focused service and process optimization,”said Lt. Governor Brian Calley. “We are early in the process. We first identified champions in different areas of state government who have some experience, plus the heart and attitude to drive changes. We’ve asked all departments for transformational ideas that will enable more efficient customer service.”
MLC lean veterans assist improvement initiatives in areas such as document management. “We spend so much time gathering and using data,”Calley said. “Our system can be more accurate, with easier access for internal and external customers.”Calley cited streamlined agricultural certification and Department of the Treasury information systems as early goals. Better integration of information systems will yield easier access to tourism as well as hunting and fishing data. “We rely heavily on partnerships with the private sector,”Calley said, noting valued assistance from MLC volunteers. “Once you are committed to improvement, so many people want to be involved and to help out.”
Humble Minds
“Companies in a lean consortium tend to be humble. No matter how far down the learning curve on lean, they share a common belief that they can still get better,”said Peg Pennington, executive director for Ohio State University (OSU) Center for Operational Excellence (COE), Fisher College of Business. “Typically, these companies continue to look outside their organization for new ideas or new ways to learn.”Under the COE umbrella, lean practitioners share and learn from others’ lean journey experiences. “Companies in organizations like this bring back new ideas to their own organizations and apply them in faster learning cycles,”Pennington said. “We provide learning opportunities in professional development meetings where a company shares how they solved a problem. Whether your company is in manufacturing, services, healthcare, etc., you can learn from others on how to improve processes in your own organization.”
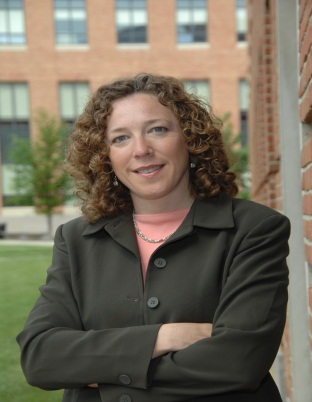
“When like-minded companies come together, we talk about how to employ lean technologies, as our organizations are trying to do more,”said COE member Alan Deutschendorf, vice president of operational excellence, Cardinal Health. “We are following the trend of professionals and organizations seeing the value of collaborating with other companies on operational excellence.”Gemba walks in member companies’ facilities and COE member visits to Cardinal sites enable networking and “give the benefit of a different set of eyes — gauging progress and seeing our blind spots,”Deutschendorf said. He also values members’ perspectives about extending lean beyond the production floor to added functional areas. Deutschendorf recommended active participation as the surest path to discovering “nuggets”or learnings that can you can take back to your organization and share with others. “Once you teach something, it can cement how well you know that topic,”he said. “You can sit in on a panel discussion, offer to do a presentation such as a breakfast talk, or sponsor a quarterly session – you’ll get more information and more into the community.”
Peer-to-peer problem solving sessions provide member value as well. “A company might call and say they have an issue with planning and lean implementation,”Pennington said. “We’ll get several companies meeting in person or on a call to discuss the problem and possible solutions.”
When COE started 20 years ago, the group sponsored four professional development events a year. Over time, program offerings migrated to focused events featuring presentations and discussions on supply chain, sustainability, IT, etc., plus problem-solving sessions and customized activities such as value stream mapping events. Members also run improvement projects with OSU students. “Our members are fantastic,”Pennington said. “They provide speakers for grad and undergrad classes, also hosting gemba and mapping sessions when students come in and can find opportunities for improvement. You’ll gain more when you open your doors to others through benchmarking opportunities, letting them see your operation, and getting your people out there to visit and learn from other companies.”
New program offerings and services are on the COE horizon. The group plans a conference next year, featuring OSU faculty sharing their areas of expertise in management science. Better information-sharing technology and research partnerships among members and OSU professors are in the works.
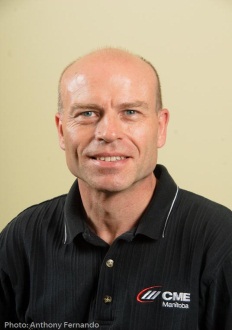
Accelerated Learning
Finding new and better ways to accelerate lean learning and create a stronger, more vibrant manufacturing base drives continuing participation in several Winnipeg, Manitoba, CN-area lean consortia facilitated by Ian Marshall, lean champion, Canadian Manufacturers & Exporters (CME) and the rest of the team at CME Manitoba. “Over the years, we’ve evolved in our programs to include more problem-solving, at least two hours in each monthly meeting,”Marshall said. A host company posts a problem and invites creative solutions from all sides. A roof truss manufacturer, for example, sought suggestions for eliminating multiple handling steps when taking parts from a saw; they received workable ideas in short order.
Meeting participants sometimes break into small groups for the problem-solving give and take. Each company representative also shares a three-minute summary of recent improvement achievements and plans for the coming month. (For another example of consortium-sparked improvements, see the box, Steel Tech: Great Ideas to Improve Your Business.)
Steel Tech: Great Ideas to Improve Your Business
Consortium idea and progress sharing sessions net significant benefits, according to Ryan Friesen, general manager at Steel Tech in Winkler, Manitoba and a member of the Southern Manitoba Lean Consortium (SMLC). Steel Tech manufactures outdoor wood- and coal-burning furnaces. “We had been looking into the purchase of a 30,000 sq. ft. shop; we were cramped in our present 14,000 sq. ft. space,” Friesen said. “We realized that with lean, we could use the space we had more effectively by making changes in material flow, batch sizes, inventory levels, etc.” Steel Tech hosted a consortium meeting, with the new plant layout as the problem-solving exercise. After touring the plant, attendees met in two smaller groups to brainstorm layout suggestions. “We took their ideas and combined them with ours to form our new plant layout, maximizing our space for production and efficiency,” Friesen said. “We can now produce twice as many units in the same amount of space and our inventory levels are much lower than they were before.” A key suggestion garnered from the consortium members: moving assembly and welding departments for continuous flow of material through the process. “It eliminated travel, which saves time, effort, and use of forklifts,” Friesen said. “We’ve sold two forklifts since we did this because we didn’t need them. The idea of placing machinery on the floor in order of use to optimize flow, which helped us, also came out of the meeting. Extra space from the new layout let us put more of the parts at the point of use instead of outside or on a shelf.” Steel Tech used to call on contractors for cutting and assembly during its peak season. The new lean layout enables the facility to handle demand spikes without contractor work. “We make more money on every unit and undertake marketing and R&D projects that may not have been possible doing things the way we used to,” said Friesen.
Marshall credits Dave Hogg, founder of the High Performance Manufacturing (HPM) consortium and a key player in many lean consortium startups, for inspiration and assistance when the Manitoba consortia began reaching out to area businesses more than ten years ago. “Dave was our mentor, and he got us going, attending many meetings here,”Marshall said. “We’ve adapted over the years, from one consortium to four; we’re about to launch a fifth.”
Hogg believes that lean consortia play a key role in contributing to corporate and individual growth by accelerating the rate of change. As improvement-focused members collaborate and share resources, they become change agents in their own organizations, he said. Hogg commented that relationships and personal involvement, more than financials and membership size, determine a consortium’s impact on organizational success.
Consortium members gain access to networking, information-sharing, and learning activities that otherwise wouldn’t exist, Marshall added. Lean consortium members trade experiences and results, holding each other accountable for progress.
Volunteer opportunities abound: Members host monthly plant tours and support informal half-day programs, special events, and out-of-region programs such as this year’s benchmarking trip to Minnesota. Approximately 40 companies and organizations (manufacturers and non-manufacturers such as a police department) belong to the initial four consortia; each one sets its own annual goals.
Learning forums and SIGs focus on topics such as purchasing and health/safety. Earlier consortium learning forums tackled lean office challenges and lean supply chain issues.
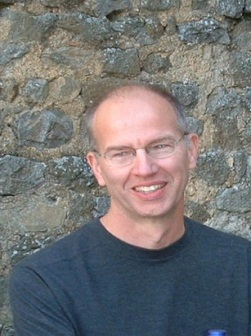
Changed Thinking
Consortium participants gain much more than just information and training on lean concepts; they learn hands-on ways to more effectively improve, said Michael Bremer, facilitator for the Chicagoland Lean Enterprise Consortium (CLEC). Deliverables include changed thinking and increased understanding about practical ways to improve a business, a holistic approach to find and fix weak areas in tool-based programs, and means to better engage employees in continuous improvement practices. Through shared learning and interaction with other members, participants learn how to fast-track performance gains. Learning cycles go faster, thanks to interaction with other member companies. CLEC is an affiliate of the Association for Manufacturing Excellence (AME).
Shared lean learning opportunities created through the Aerospace Components Manufacturers in Connecticut created broader understanding that “lean is the way you do business,”said Allen Samuel, executive director. Members (many are competitors) gained knowledge working together through activities such as lean training sessions partially funded through state grants, visits to fellow members’ facilities, presentations and discussions about everything from lean implementation issues to vetting kaizen facilitators.
Lean Consortia “Lessons Learned”
Want to start a lean consortium or gain more from your participation? Here are “lessons learned”from experienced lean consortium folks.
Julie Simmons, Northwest High Performance Enterprise Consortium (NWHPEC):
- For a startup, begin with three to five companies. Identify common needs, fill those needs as fast as possible, and then keep asking questions such as, “How do I know what I need to learn?”
- Think creatively about facilitation and administrative needs, not hiring staff right away. Perhaps a resource is available several hours a week to facilitate planning, events, and other activities.
- Be cautious about applying for grants or government funding; don’t get bogged down with bureaucracy.
- Don’t expect a consortium to solve all your problems. Be open to different ways of learning, from a foundry or other organizations and industries.
Joe Krall, finance manager, Jacksonville Lean Consortium (JLC):
- People need to see a compelling reason, or value proposition, to participate. Find out what they are passionate about, what keeps them awake at night. Push the envelope; for example, brainstorm ways to apply lean concepts in sales.
- Participation is a must for senior leadership and others in member organizations.
- Develop realistic goals for the consortium. Mature lean organizations can help lean beginners by sharing their passion and learnings about creating and sustaining successes.
- Reach out to other resources and consortia, ask for feedback about challenges.
Teresa Hay McMahon and Gina Singer of the Iowa Lean Consortium (ILC):
- Develop the consortium’s purpose, vision, and mission – but don’t take forever. At some point, just get started, test programs, and learn more about members’ appetites for shared learning.
- Create your own particular lean consortium spin designed to serve your members; ensure that you are filling a need that is not already served.
- Recruit a cadre of dedicated volunteers when you’re starting from scratch, then nurture broader participation over time.
- Benchmark against other organizations; they are willing to share.
Debra Levantrosser Setman and Julianne Leigh of the Michigan Lean Consortium:
- For a startup, develop a core nucleus of dedicated volunteers who will get the group up and running, then prepare for future resource needs.
- Create a shared vision, a financial plan, and bylaws.
- Link with other existing groups – educational, economic development, professional, etc. for broader perspectives.
- Recognizing that members represent many levels of lean understanding, provide a range of collaborative, fun learning and participation opportunities.
- Avoid mission creep. Collaborate with other groups when shared initiatives support your group’s mission and goals.
- Develop a plan for running an all-volunteer organization. Rewards, recognition, and motivation are critical elements.
Peg Pennington, Ohio State University (OSU) Center for Operational Excellence (COE), Fisher College of Business:
- To start a lean consortium: Begin with a plant tour, asking people what they saw and learned. Based on feedback, plan your next meetings, developing a monthly or quarterly cadence. Involve senior leadership in participant organizations.
- Keep a lid on costs, remembering your mission, and that people come to meetings for learning.
- Ultimately the consortium is about having a relationship with people. Continue to attract and retain dedicated people, then plan programs focused on their needs. Sustainability, for example, draws increasing member interest.
Ian Marshall, Manitoba Consortium for Manufacturing Excellence (MCME), Manitoba Consortium for Operational Excellence (MCOE), Manitoba Consortium for Sustainable Improvement (MCSI), and Southern Manitoba Lean Consortium (SMLC):
- As a consortium member, be committed to continuous improvement in your operation, and understand that you will gain the most value by sharing, not just receiving from others.
- Designate one primary representative (preferably senior leadership) and someone as backup, to keep participation flowing. At least twice a year, hold a consortium senior leadership meeting – their involvement is critical.
- Volunteer for facilitator and meeting coordinator roles.
- A coordinator (possibly part-time) can shepherd event planning and other tasks. Each Manitoba consortium also hired a part-time mentor/facilitator who visits member companies, sharing counsel and problem-solving expertise.
- Consortia are not for the faint-hearted. Like lean, you can dabble or you can be serious. Successful consortia require significant effort and continuing, customer-focused improvement.
Virtual Lean Learning Experience (VLX)
A continuing education service offering the latest in lean leadership and management.