As we plan our annual Lean Summits, we always try to develop a theme that resonates with the needs we sense permeating the community. For example, in 2018, at LEI’s 10th annual Lean Transformation Summit, employers from manufacturing, R&D, healthcare, and services addressed the theme How to be a Better Employer, sharing their experience trying to be lean employers in plenary addresses for the Summit’s 700 attendees.
Everywhere we go, executives tell us that their biggest challenge is finding and keeping excellent people. Of course, we can’t easily solve all the problems involved in the job market’s supply and demand or health, but we can do a lot about the “keeping” and the “excellent” parts. So, if excellent employees don’t seem to be accessible in your available talent pool, the right question to ask (the problem to be solved, the job to be done) is: What can we do to make all our employees excellent?
… if excellent employees don’t seem to be accessible in your available talent pool, the right question to ask … is: What can we do to make all our employees excellent?
What is a ‘Lean Employer’
Jim Womack, LEI’s Founder and Senior Advisor, burned some midnight oil on some crucial work to articulate a new set of thoughts around the question of just what a lean employer is. In “Jim Womack on What Makes for a Good Lean Employer,” you can read his insights. In the article, Jim shares a few behaviors and practices that a “lean employer” would adopt. They include: introducing daily management starting with frontline work to create basic stability, performing hoshin planning to identify and prioritize your biggest problems/opportunities, continuously improving every value-creating process through kaizen, protecting your employees (through social heijuka — predictable schedules, full-time work, and steady work during the downturns), and stop making employees the “shock-absorbers for the business.”Jim also introduces the idea of the Virtuous Spiral of Lean Employment, which I have turned into this graphic representation:
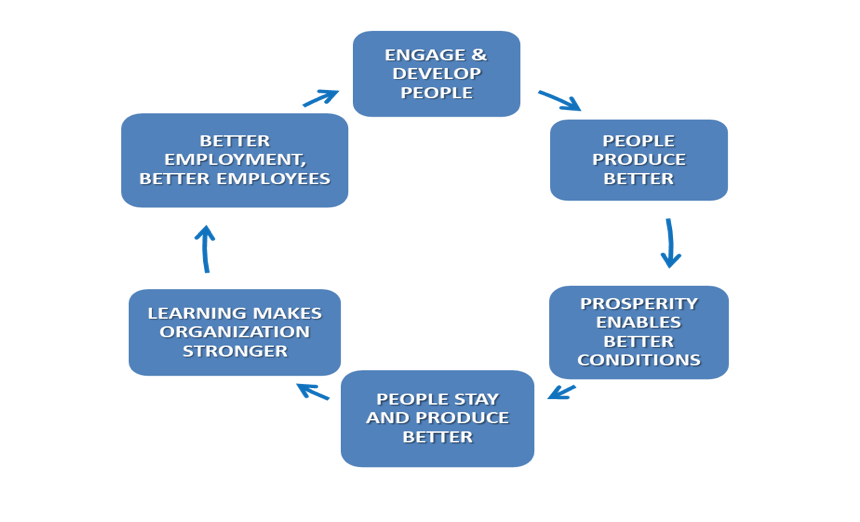
A Riveting Keynote
Among the year’s practitioner keynotes was my new favorite conference keynote of all time. Dr. Kiame Mahaniah, CEO of the Lynn Community Health Center (LCHC), spoke about the work of this small center in the economically, culturally, and socially diverse community of Lynn, Massachusetts. The challenges faced by Kiame, LCHC, and the entire Lynn community are immense.
In his address, Kiame and his predecessor Lori Berry (in video clips) described LCHC’s lean journey and how they managed the CEO transition. As described in his presentation, their journey addressed the ambitious question: “How do we transform a whole community by transforming its biggest asset, the health center?”
Regarding the CEO transition, above all, they prove that a lean transformation can survive a CEO change. Lori and Kiame decided on the radical approach of cooperating in a planful way to transition as seamlessly as possible from CEO A to CEO B, preserving the excellent lean transformation work that began two years ago. Colleagues Bernadette Thomas and Kim Eng, LEI Coach Alice Lee, and the LCHC team supported their efforts.
Kiame also briefly shared four critical points that help ensure a successful CEO transition:
- Trumpet lean successes – While maintaining the humility Lean Thinkers are known for, you must ensure all the stakeholders know that you attribute the organization’s successes to lean thinking.
- Identify people with twin but conflicting personality traits — “who are willing to admit that things are a total mess and yet be able to believe that it can be different.”
- Set up lean thinking and practices as “a source of independent authority and wisdom to which you as the CEO, as a leader, can be held accountable.”
- Begin succession planning on Day 1.
Another Insight
My favorite quote of the event came from Tyler Shilling, CEO and founder of the Shilling Robotics division of TechnipFMC. He shared his trials and troubles escaping the trap in which he had placed himself as the answer man for every vexing problem his employees faced. Upon being continually pressed for yes or no answers and squirming away from being cornered into giving overly simplistic responses, Tyler came up with, “I am generally in favor of things that work and not in favor of things that don’t work. Now, please figure out which among your options has the greatest chance of working better than the others.” A great example of true set-based thinking!
This year’s Lean Summit 2023, on March 8 and 9 in Tucson, promises to have similarly enlightening keynotes and other presentations, which will explore the theme of Celebrating 25 Years, Charting Next-Generation Lean Thinking. In addition to the in-depth and inspirational learning experience you’ve come to expect from the Lean Summit, this year’s event will feature a glance back to the past, honoring and celebrating the 25th anniversary of the Lean Enterprise Institute. As part of this reflection, this year’s gathering will feature a special focus that gets to the heart of lean thinking: developing leaders and team members.
Editor’s Note: This Lean Post is an updated version of an article published on May 15, 2018.
Virtuous Spiral of Lean Employment, the produced graphics is excellent, also like the four critical points of the transition,
great post
thank you