Photos courtesy of Results Washington
While the lean community has a history of contributing to social good, until recently it hasn’t been recognized for doing social good. And at LEI, for the most part we haven’t spoken about ourselves this way. Lean is still largely considered an improvement methodology used in manufacturing to reduce costs and improve quality. It’s often misunderstood as being solely about efficiency (not effectiveness) gained through the use of tools and process improvement projects, often doing harm to both employees and community members whose organizations want to “go lean”. And unfortunately, some organizations do use Lean this way.
As a result, in many circles Lean has an image problem.
Our view at LEI is that lean thinking and practice helps organizations create more value with less waste: time, human effort, capital, space, defects, and rework, etc. by focusing on the real “work” to be done and asking what type of management and management system is needed to get the work done in the best way. It’s about embracing the challenge of systematically developing people to solve problems and consuming the fewest possible resources while continuously improving processes to provide value to community members and prosperity to society.
What We’re Observing
While the lean community has been growing, the field of social impact – with social impact as its organizing principle – has risen in influence. Today, many young people of the millennial generation (20 and early 30 somethings) across the political spectrum are leaving college with the desire to work in fields of social entrepreneurship or social change. This is not unlike the children of the ‘60s who heeded President Kennedy’s call to public service – both within government and nonprofit organizations – to address emerging social problems.
We’re seeing young people build organizations (nonprofit and for-profit) based on lean and Lean Startup principles. We’re seeing large, established organizations looking to better understand what lean thinking is all about in order to do better by their employees and customers. And here’s another thing we’re noticing: the senior “social good” generation and younger “social good” generation may be split across generations, organizational structures, and experience level. They may use different language to describe themselves and have different knowledge and skills. But they have the same desire to “do good” and solve problems in common.
On the ground, the lean community is busy trying to improve how work is accomplished, focusing on ways to better deliver products and services that are valued by stakeholders in both for-profit and nonprofit organizations. Increasingly, we see the lean community moving into “public service” fields:
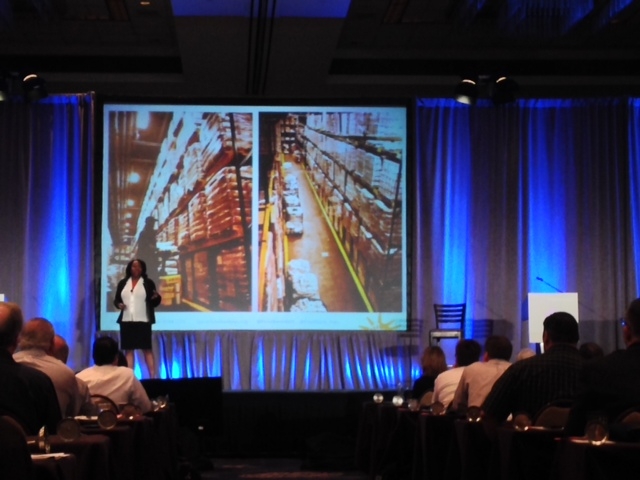
- The Toyota System Supplier Support Center (TSSC) has collaborated with Food Bank For New York City (a nonprofit serving 1.5 million New Yorkers annually) to rethink and improve Food Bank’s operations, top to bottom. Read more about their work in The New York Times.
- Lean Impact and The Lean Startup Conference have convened gatherings and created workshops on lean for social good, exploring how to adapt Lean Startup principles to the unique challenges of nonprofits and social enterprises alike.
- In 2013, here at LEI, we developed a partnership with the State of Washington to learn about how they were introducing lean thinking into operations and how we can help. Supported by Governor Jay Inslee, Darrell Damron and Hollie Jensen have emerged as spokespersons for how a state can use lean thinking in the public sector. Damron and Jensen shared their State’s journey at LEI’s annual Lean Transformation and Coaching Summits. (Learn more about “Results Washington” in Damron’s Lean Post and Roberto Priolo’s interview with the Washington’s leadership team on Planet Lean). LEI has been working with Damron and Jensen to introduce lean as an enterprise-wide, transformation strategy and management system, and Results Washington is now using LEI’s Lean Transformation Model as a framework to organize and communicate its lean strategy.
- In Gemba Walks, LEI Founder Jim Womack is writing on how society and organizations can tackle the problem of sweatshop labor by improving their production and people systems. By doing so, companies stay competitive while protecting workers from abuse and unsafe work conditions.
Thinking Towards What’s Next
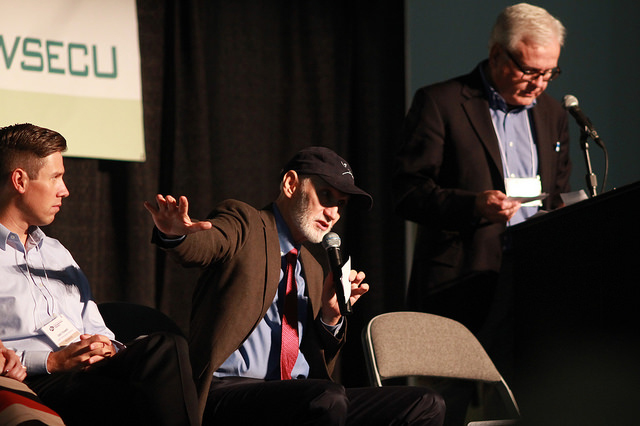
These are just a few reasons why in 2014 we decided to investigate the need for, and feasibility of, a Public Service Value Network (PSVN) – loosely modeled after the learning and development of a community of practice that led to today’s Healthcare Value Network, first established in 2008.
The Healthcare Value Network emerged out of LEI’s partnership with one of the country’s leading healthcare organizations, ThedaCare Center for Healthcare Value in Appleton, Wisconsin, in response to national problems in healthcare delivery (i.e. cost, quality, timeliness, access, etc.). The launch of this network was based on a foundation a community of leaders and practitioners who saw the results of a new way of thinking about and practicing healthcare delivery. Members saw the value and expressed a willingness to share and learn from one another. Why reflect on this particular network or story? Because, beyond manufacturing, the improvements in healthcare are the most successful examples of a lean “spin-off community” we’ve seen yet. In building PSVN, we want to learn from their example.
The objectives of LEI’s Public Service Value Network are to a) better understand the problems and needs these organizations are facing and experiencing and b) learn how public service agencies and organizations in the social service space themselves are attempting to improve by going to see their lean activities whenever possible. (In other words, “be lean” about supporting new lean applications and the development of new lean communities of practice.)
We’re also reaching out to other organizations in the public service world – government agencies, foundations, nonprofits, NGOs – to understand what work is already being done and what experiments people are running. With regard to government, fortunately for the citizens of the United States, the lean movement is rapidly spreading through all levels – federal, states, counties, and municipalities, as well as the nonprofit sectors at home and abroad. Our purpose in working with these organizations is to show that lean is not a program of tools, process improvement projects, random kaizen events, or training activities focused on certifications and belts. Training and capability development should be integrated with continuously improving the work by developing problem solvers at all levels. And leadership must exhibit behaviors – and support a management system – focused on developing people who know how solve problems, work effectively with other parts of the organization, identify real needs, and deliver on purpose.
We believe the Lean for social good movement goes far beyond reporting improvement metrics, reductions in processing steps, or reducing the time it takes to get a license. Lean is a way to improve the lives of individuals and communities, whether that’s preserving and creating quality jobs; bringing together children in need of a loving home with couples who are able to provide one; providing food services to struggling, proud families with dignity; helping startups and social enterprises build sustainable businesses that treat people well; or improving education processes so more time is spent developing and coaching future generations.
We’re in the process now of exploring partnerships with organizations already doing work in this social good space. We want to learn from you, share stories, and collaborate with you. Please share your successes, challenges, ideas, and thoughts. We’re also looking to connect with leaders and change agents who would like to participate in this budding community of practice.