Upwards of 80% of the cost (and hence, waste) is committed for a new product or service by the time product and process designs get locked-in during development before operations even builds one part. Instead, many leaders still choose to focus the majority of their improvement efforts where 80% of the cost is incurred – the operational value stream, post-launch. One can’t help but ask, why don’t organizations focus more creative lean design energy within the product development value stream?
For one organization (let’s call them Acme Devices) that has been working to improve their operations for many years, the cycle of adding value by reducing waste started to resemble squeezing water from a rock. This meant stalled progress. Frequently Acme would get 10-20% operational improvements, but the actions that got them there were difficult to sustain and even harder to further improve. Acme Devices realized that what they originally thought was kaizen (continuous improvement) was really just touzen (correction of a design) and rework around a poorly configured new process.
Why didn’t Acme Devices focus more on lean within process development?
Here are the three causes they discovered (unfortunately, these are all too common):
- Too Little, Too Late: No upfront process thinking and process design for new products or services before their final design.
- Too Much, Too Early: Critical operational decisions are made too soon with incomplete knowledge or inaccurate input and cannot be changed later on.
- Penny-Wise, Pound-Foolish: Functional or area decisions are made that may lead to local optimization but frequently lead to overall performance reduction.
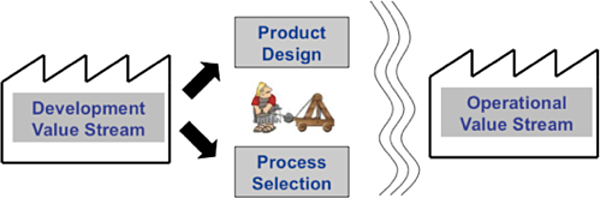
From Waste Reduction to Waste Avoidance (Prevention is the best cure!)
Eventually, Acme Devices managed to move upstream in the product lifecycle to the product development value stream to shift the focus from waste-out to value-in. While it was daunting to know where to begin upstream from operations for lean in development, Acme chose the starting point of process creation for new products. Acme selected two critical new product development programs to pilot upfront process development and design.
After studying the methods of leading lean organizations in automotive, aerospace, and other industries, Acme leaders discovered that successful lean process creation within the development system required the following:
- System Architect: Find a System Architect who will be responsible for thinking about the whole value stream and its processes in conjunction with the product design.
- Team of Responsible Experts: This System Architect should lead a team of responsible experts who have a mastery of available / emerging technical and operational knowledge.
- Repeatable Routine for Creating Lean Processes: This team develops a Lean Process Creation (LPC) methodology that becomes standard engineering work in the “Development Factory” for all new products.
- Rapid Learning Cycles: Utilize the Set-Based Concurrent Engineering (SBCE) methods that “test before design” for multiple alternatives before converging to the optimal process design that needs to be configured.
Following this methodology in pilot areas, Acme realized step-wise improvements to health and safety, first-time quality, value stream lead time, on-time delivery, and cost.
In the past, improvements after launch would have yielded only 10-20% performance gains with substantial resources doing the work. Now, an upfront lean process resulting in them capturing 30-50% gains from initial process concept to final configuration prior to launch. Plus, the process creation teams generated many valuable ideas they could use toward future product and process design enhancements for their next generation product. For the engineering organization, this justified “front-loading” the design resources within the product development system. Acme Devices now had evidence that such an investment was required to launch truly lean processes from the start.
Next time your organization is ready to design a critical new product or add capacity, move upstream with lean process creation. This is a good first step toward meaningful, lasting results and real lean transformation.
Need more help getting started? Read Lean Product and Process Development, 2nd Edition by Allen C. Ward and Durward Sobek.